Over ons
Innovaties voor klimaatvriendelijke productie
Klimaatbescherming zit stevig verankerd in BASF's nieuwe strategie. Om onze CO2-uitstoot drastisch en op de lange termijn te verlagen, hebben we volledig nieuwe lage-emissie technologieën nodig. In het Carbon Management R&D-programma brengen we alle projecten samen die focussen op de chemische processen van de toekomst.
Kraken op elektriciteit
Aan het begin van ieder productieproces in de chemische industrie moet de basisgrondstof nafta worden ‘gekraakt’. Kraken betekent dat de nafta wordt verhit onder temperaturen tot 850° C, waardoor onze basischemicaliën zoals ethyleen, propyleen en benzeen ontstaan. Dat kraken gebeurt in onze stoomkraker.
Door de hoge temperaturen die nodig zijn in de stoomkraker, verbruiken we energie en komt er CO2 vrij. We onderzoeken nu of het mogelijk is om de stoomkraker te elektrificeren met groene stroom waardoor de emissies met 90% zouden kunnen dalen.
We werken niet alleen aan een concept voor elektrische krakers maar onderzoeken ook welke materialen de hoge elektrische stroom en temperaturen aankunnen. We werken daarvoor samen met overheden en vijf andere internationaal opererende chemiebedrijven in België, Nederland en Duitsland.
![Steam cracker II, the largest individual plant at BASF's Ludwigshafen site, covers a surface area of about 64,000 square meters, which is about the size of 13 soccer fields. The steam cracker is also the heart of BASF's Verbund production strategy. This giant plant has been operating since 1981 and uses steam to crack naphtha at about 850°C [1,562°F]. This process leads primarily to ethylene and propylene, both indispensable feedstocks for manufacturing numerous products in Ludwigshafen. Steam cracker II, the largest individual plant at BASF's Ludwigshafen site, covers a surface area of about 64,000 square meters, which is about the size of 13 soccer fields. The steam cracker is also the heart of BASF's Verbund production strategy. This giant plant has been operating since 1981 and uses steam to crack naphtha at about 850°C [1,562°F]. This process leads primarily to ethylene and propylene, both indispensable feedstocks for manufacturing numerous products in Ludwigshafen.](/api/imaging/focalarea/original/210x/dam/jcr%3A9c47c704-e499-33c4-b65c-aefcc2e140f1/39_1510_Steam_cracker_at_BASF_Ludwigshafen_site.jpg)
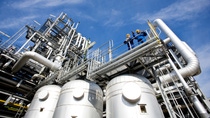
Waterstof zonder CO2
We hebben waterstof nodig om andere producten te maken, zoals ammoniak. Maar bij de huidige productiemethode op basis van methaan komt CO2 vrij. Daarom ontwikkelen we procestechnologie om waterstof te maken op basis van aardgas. Daarbij komt geen CO2 vrij. De technologie splitst aardgas namelijk direct in zijn componenten waterstof en koolstof. De koolstof kan gebruikt worden in bijvoorbeeld staal of aluminium. De technologie om waterstof te maken - methaanpyrolyse - heeft minder energie nodig dan momenteel het geval is. Als die energie uit hernieuwbare bronnen komt, kan waterstof op industriële schaal gemaakt worden zonder CO2-emissies.
Klimaatvriendelijke methanol
Methanol is een belangrijke basisstof voor veel van onze producten. Gewoonlijk wordt methanol gemaakt van syngas, dat tot nu toe hoofdzakelijk werd verkregen uit aardgas. Met behulp van speciale katalysatoren kan dit vervolgens worden omgezet in ruwe methanol, die na zuivering verder kan worden verwerkt. In het nieuwe BASF-proces wordt syngas gegenereerd door gedeeltelijke oxidatie van aardgas, wat niet leidt tot uitstoot van CO2. In de volgende stappen van het proces wordt methanol geproduceerd uit syngas. Restproducten die hierbij vrijkomen, worden omgezet in CO2 dat vervolgens wordt behandeld met waterstof (die we ook CO2-vrij willen produceren via methaanpyrolyse). Hierbij ontstaan dan weer grondstoffen die kunnen worden gebruikt aan het begin van het syngasproces. Als dit proces met succes op industriële schaal kan worden toegepast, zal er bij het gehele productieproces – van syngas-productie tot zuivere methanol – geen CO2 meer worden uitgestoten.
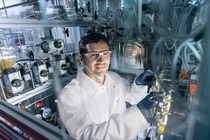
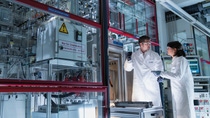
CO2-vrije olefinen
Olefinen zijn de grootste groep van intermediates in de chemische industrie. Bij hun productie komt er echter CO2-uitstoot kijken. Momenteel worden olefinen geproduceerd op basis van nafta. Als we nafta vervangen door methaan kan er uitstoot vermeden worden.
Bovendien hebben onze onderzoekers een nieuwe krachtige katalysator ontwikkeld waarmee syngas kan worden geproduceerd door een combinatie van methaan en CO2. Via een tussenstap kan dat syngas op zijn beurt worden omgezet in olefinen.