Qui sommes-nous ?
3D-Printed Concrete Formwork
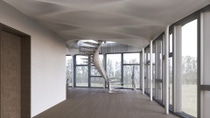
3D printing allows highly complex formwork to be created for walls or facades that would otherwise be impossible or incredibly difficult.
The BASF experts from the Scouting & Academic Collaborations unit in Dübendorf, Switzerland, are combining their know-how with the excellence of Swiss research institutes and other industrial partners. The result is a boost to innovation in the field of digital architecture.
Strong and highly capable yet light and easy to form into many different shapes, the high-performance material that is concrete is taking on another dimension in the age of digital planning and manufacturing. Seamlessly linking digital technologies to the physical construction process makes it possible to implement a hitherto inconceivably wide variety of shapes in architecture and can be pivotal in improving efficiency in production and the sustainability of buildings. Custom-made formwork can be produced with a 3D printer and then poured with concrete mixtures optimized for this purpose.
Innovative collaboration on digital planning and manufacturing
Working with two academic research partners and other industrial partners from various stages of the value chain, BASF has managed to turn an idea for concrete formwork into a very impressive model project within a short space of time. The cooperation includes ETH Zurich, which not only plays a leading role in the Swiss National Science Foundation's (SNSF) National Centre of Competence in Research Digital Fabrication, but is at the forefront of the development and integration of digital construction technologies worldwide. Empa, the Swiss Federal Laboratories for Materials Science and Technology, is another prestigious cooperation partner that bridges the gap between academic research and industrial applications.
BASF contributes to this cooperation not least through the comprehensive set of skills in 3D printing brought to bear by the team from BASF 3D Printing Solutions GmbH. Its innovative scan-to-print system opens up the possibility of manufacturing form-active and self-supporting building elements with much less material than usual – up to 70 percent less despite maintaining the same strength. This is helping to make construction smarter, easier and more sustainable.