Change for climate
If insulated walls could talk…
They’d tell you about the innovative housing materials that are making it possible to heat and cool homes using less energy. By reducing domestic carbon footprints, our high-performance thermal insulation materials are helping protect the climate and homes all over the planet. That’s why they’re being used in Containerwerk’s ‘tiny houses’ made from upcycled shipping containers.
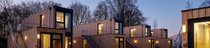
The inspiration: a future we can live in
For thousands of years, we’ve built ourselves places where we feel cozy, dry, and secure. But, however comfortable we feel within our own four walls, what’s happening to our planet cannot be ignored. Due to the environmental impacts of climate change, the growing frequency of extreme weather events, and soaring energy prices, future-proof construction is a real necessity.
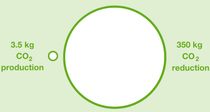
1 kg of PU insulation creates 3.5 kg of CO2 in production, but reduces 350 kg of emissions over a 50-year lifetime.
Source: PU EUROPE excellence in insulation – Factsheet 13/1
Containerwerk: thinking inside the box
Containerwerk is an amazing company that creates sustainable living spaces from upcycled shipping containers. The containers are “modular”, which means they can be stacked and arranged in different ways to create larger or smaller buildings. Of course, shipping containers would be completely unsuitable as accommodation without effective insulation.
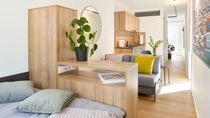
Containerwerk’s tiny houses are built with Elastopor to achieve the highest levels of insulation in even the smallest spaces.
This is where BASF comes in. We custom-designed the formulation of our Elastopor® insulating system to fit exactly to Containerwerk’s needs, providing them with a very thin insulation layer to turn those metal boxes into residential modules that can be heated efficiently. This increases the space for living and importantly, cuts wasted energy to help protect the climate.
The thinking: better insulation, less energy
Well-insulated homes reduce the amount of energy needed for heating and cooling. The householder benefits because it costs less to ensure a comfortable living space. The climate benefits because greenhouse gas emissions, known contributors to global warming, are reduced. BASF’s Elastopor and Elastopir® PU rigid foam insulation systems are helping the global construction industry deliver buildings that are both comfortable and energy efficient all over the planet – from tiny houses to an Antarctic research station.
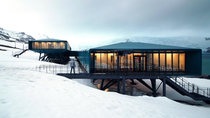
A research station on King George Island in the Antarctic benefits from BASF insulation materials.
The innovation: Elastopor – high-performance in thinner layers
Our scientists have spent more than two decades continuously improving the thermal performance of these versatile insulation materials. They can be tailored to living and working spaces anywhere, regardless of building size, location, environment or climate – reaching high levels of insulation with thinner layers and ensuring that even the smallest buildings meet official safety and energy efficiency standards.
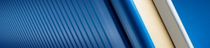
Sustainable manufacturing: reducing your footprint… and ours
BASF is also applying a new approach to manufacture our insulation systems in a more sustainable way – the Biomass Balance (BMB) approach. The BMB process replaces fossil resources used in manufacturing with 100% renewable materials such as bio-naphtha or biomethane derived from organic waste, crops or vegetable oils.
Learn more about some of our BMB insulation systems: