Media
Fertilizer out of thin air
In September 1913, the first industrial-scale ammonia production plant came on stream at BASF in Ludwigshafen
Even a hundred years after the celebrated beginning of the industrial production of the basic chemical ammonia, a visit to BASF's two ammonia plants in Ludwigshafen still impresses. Standing in front of the approximately 20 meter high reactor of the older plant and reflecting upon the elemental forces that cause nitrogen and hydrogen to react and produce ammonia brings home the importance of this scientific and technical breakthrough. The Haber-Bosch process for ammonia synthesis, which was first successfully operated here in September 1913, was the decisive step into the age of mineral fertilizers. This innovation became a key driver in the development of the industrialized society and is still securing the nutrition of billions of people today. The high pressure reactor in front of us is a great-grandchild of the apparatus developed by Carl Bosch, much larger of course but of similar design. The newer plant next door with its more advanced process technology exhibits less visible historical similarities. The two ammonia factories together produce more than 2,000 metric tons per day of the much sought-after compound NH3.
"The realization of industrial ammonia synthesis involved high entrepreneurial risks and demanded great staying power," emphasizes Production Manager Michael Mauß. "Processes and equipment for this pioneering technology had to be developed from scratch." This audacious approach provided the growing chemical company BASF with a second important mainstay: the manufacture of dyestuffs, previously the company's main activity, was augmented by the production of fertilizers. "The experience gained with the high pressure technology and the advances achieved in catalysis research in the following decades enabled the development of further innovative production methods such as methanol synthesis," adds Mauß. And the close cooperation between chemists and engineers in developing complex processes, the symbiosis of science and technology, became the guarantor of BASF's continuing success.
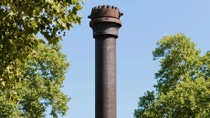
The foundations for the "Synthesis of ammonia from its elements" were laid by Professor Fritz Haber from 1904 onwards with his work at Karlsruhe Institute of Technology. The industrial upscaling of ammonia synthesis entrusted by BASF to Carl Bosch in 1909, however, initially raised unforeseen problems. Because the high-pressure process required pressures and temperatures considerably exceeding those that had so far been technically possible. The first plants couldn't stand the strain and its steel reactors burst. Bosch the chemist, who was experienced in metallurgy, closely studied the metals that had been used and finally identified the cause: the hot, highly pressurized hydrogen was taking the carbon essential for strength out of the steel walls, making them soft and simultaneously brittle. Bosch overcame this challenge by fitting the inside of the apparatus with a thin lining of low-carbon soft iron and drilling holes in the pressure bearing steel wall. This allowed the hydrogen that had penetrated into the material to escape without causing damage. This innovative high pressure technology required further components that were not available anywhere, and had to be designed and tested within the company. BASF established the chemical industry's first material testing facility for this purpose in 1912.
"Even today, the industrial production of ammonia is still operating at the limits of the possible. The challenges for the material and technology of the production plant are enormous under these high pressure synthesis conditions," explains Dr. Jürgen Korkhaus, Head of Materials Engineering, comparing present with past practice. "Even minor variations in the process can subject the materials to immense stresses. The apparatus therefore has to be designed and constructed with extreme care." The reactor of the newer ammonia production plant in which the synthesis gas mixture reacts over a catalyst bed at above 400 degrees Celsius and more than 150 bar pressure to produce ammonia, has a 15 centimeter thick wall of high-strength steel. Its advanced alloy resists the pressurized hydrogen, making the legendary casing unnecessary today.
The raw material used to generate the synthesis gas is also different today: in the first few decades of the Haber-Bosch process, a large number of employees prepared a bed of glowing coke and passed steam over it. Today, ammonia plants use natural gas as a feedstock and energy source, which also makes up the lion's share of the production costs. At Ludwigshafen site, the ammonia production is the second largest natural gas consumer after the company's own power generating plants. As in the early days, the necessary nitrogen is obtained from the air supply and, for a change, costs nothing at all.
The industrial synthesis of the basic chemical ammonia has become an essential part of the production Verbund. At BASF in Ludwigshafen, this material is now used mainly to manufacture urea-based glues and impregnating resins for wood-based materials, but also various amines and caprolactam, the starting material for polyamide plastics. Worldwide, however, three quarters of the generated ammonia is still used for the production of fertilizers.
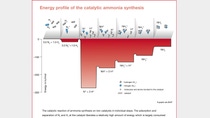
The Info Box
Nitrogen compounds as fertilizers
As an important nutritional element, nitrogen plays a vital role in plant growth. The plants absorb it mainly in the form of nitrate or ammonia. The amount of fertilizer should be matched exactly to the plant's requirements and the condition of the soil. Various nitrogen compounds are used in fertilizers in the different regions of the world; here are some prominent examples:
Ammonium sulfate
Most of the ammonia produced by BASF's first production plant was initially processed into ammonium sulfate. This ammonium salt was already known to agriculture as nitrogen fertilizer but its availability was limited. It can be manufactured either directly through a reaction with sulfuric acid or by using gypsum slurry (calcium sulfate).
Ammonium sulfate nitrate
A successful mixed salt fertilizer with a higher nitrogen content of about 26 per¬cent is ammonium sulfate nitrate. This is obtained by mixing the ammonium nitrate obtained from the reaction of ammonia with nitric acid and the afore¬mentioned ammonium sulfate in a ratio of two to one. Initial problems with storing the mixed fertilizer resulted in a tragic explosion accident in Ludwigshafen-Oppau in 1921.
Calcium ammonium nitrate
A fertilizer that combines the fast acting nitrate nitrogen (ammonium nitrate) with a calcium component (calcium carbonate) is calcium ammonium nitrate. The calcium counters acidification of arable soil. The fertilizer was initially produced using limestone powder, and later also the converter lime obtained during production.
Urea
Outside Europe, urea with its nitrogen content of 46 percent has traditionally played an important role as a fertilizer. This classical product of organic chemistry can be synthesized from ammonia and carbon dioxide under high pressure. The world's first industrial scale plant for continuous production of urea went into operation at BASF in Ludwigshafen in 1922.