Charging ahead with BASF’s light stabilisers
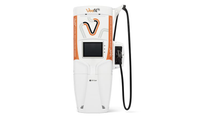
Next time you drive past an electrical vehicle (EV) charging station, take a second look at the brand name. If the battery high powered charger (HPC) is a Tritium, then you might be interested in knowing the durable and shiny plastic the charger is housed in contains BASF’s UV light stabilisers.
This plastic is produced by Brisbane-based manufacturing company EGR, a customer BASF first collaborated with to produce polycarbonate sheets, the material commonly used on out outdoor plastic roofing. When EGR were designing a durable plastic for Tritium’s HPC stations that needed to endure all weather conditions, adding BASF’s market-leading light stabilisers to the mix was an important inclusion.
“UV stabilisers extend the life of plastic by chemically stabilising the polymer and blocking UV light from the sun,” explains Yvonne Mah, Business Development Manager Plastic Additives. “This is needed because ultraviolet light can initiate chemical reactions in polymers which result in discoloration and the breakdown of chemical bonds and loss of physical properties”.
“Our stabilisers also improve manufacturing productivity with low volatility, better chemical resistance and wide product stewardship compliance and are environmentally friendly during the manufacturing process,” she adds.
Tritium is a world leader in electrical vehicle charging technology. Headquartered in Brisbane, Tritium export their products globally with EV charging stations in Europe, America and Australia (including in the carpark of the BASF lab at Monash University).
With more electric cars expected to enter the commercial market in the coming years, this collaboration is an exciting venture for BASF to be a part of.