Turning junk into jobs
Discarded bottles, plastic bags and food cartons – piles of garbage are a huge problem on the streets of Lagos, Nigeria. The city generates around 5 million metric tons of waste every year, but only 70 percent of it is collected by authorities. Wecyclers has built a rewards-for-recycling program, enabling people in low-income communities across the Lagos metropolis to capture value from recyclable waste.
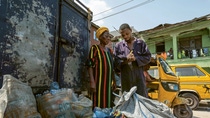
Getting the waste off the streets: When Wecyclers was founded in 2012, it collected recyclables from a network of households and communities by bike. As the business has grown, motorized tricycles, vans and trucks were added to the fleet. People get points for every kilogram of material they provide, which they can swap for cash rewards. Subscribers can use a mobile app to request a pickup, and to track the points they have earned.
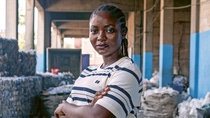
Wecyclers vehicles deliver their loads to one of the company’s three collection and processing hubs in the city. Rafiat Ayoola is the operations lead at the largest hub. She interned at Wecyclers as a student and became a full-time employee in 2016.
Today, Rafiat Ayoola is responsible for the supervision of around 50 on-site employees and is also involved in the training and onboarding of franchisees, helping them establish new collection hubs and ensuring they have the knowledge and equipment they need to run a successful business.
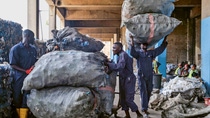
At the hub, materials are weighed, separated, and taken to sheds dedicated to the handling of various material categories. “The range of materials we handle has expanded,” says Rafiat Ayoola. “We now collect glass bottles, for example, and we are working with BASF on a project to recycle polystyrene packaging. It’s the first time that has been done in Nigeria.”
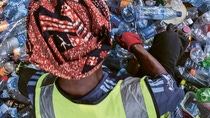
Staff at the hub begin processing materials as soon as they arrive at the shed. PET bottles are sorted by color, and caps and labels are removed to produce high-quality, consistent batches that are suitable for mechanical recycling.
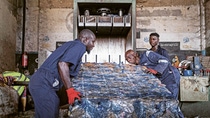
Sorted materials are compressed into 300-kilogram bales, so they are easier to handle and store on the site. “It makes a big difference, because one bale of PET bottles contains as much material as 14 bags,” says Rafiat Ayoola. Materials are taken from the site to local manufacturers, where they are transformed into a wide range of products, from tissue paper to furniture.