News & Media
Low carbon footprint insulation using BASF's Neopor® BMB
First major renovation project with energystore+ successfully realised
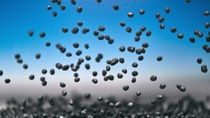
In the production of Neopor® BMB, fossil raw materials are replaced by renewable ones at the beginning of the value chain
In a UK industry first, energystore has launched a new low-carbon footprint insulation product range, energystore+, which combines climate protection with high product quality. With these products, energystore will provide a significant opportunity for their customers to reduce the carbon footprint of their buildings. In general, insulation of buildings, whether new construction or renovation, is essential for the reduction of carbon emissions. As a result, building owners can save energy and heating costs and gain comfort as houses heat up faster and stay warm for a longer time. In Summertime, insulation helps to keep houses cool.
The energystore superbead+ system is an injected EPS foam bead designed for use in multiple cavity wall scenarios including masonry, party wall and timber frame. energystore TLA+ combines EPS foam beads coated in an innovative additive with cement to create a pourable insulation for use in floor and roof construction. Both energystore+ products are based on expandable polystyrene (EPS) granules Neopor® BMB, produced by BASF.
Connor McCandless, energystore Group Sales & Innovation Director, says “After working with BASF over the last 18 months on this project we’re thrilled to bring energystore+ to our customers. We believe that future construction projects need to reduce carbon emissions. The energystore+ range gives a fantastic option for our customers to make their next project as sustainable as possible.”
Neopor® BMB used for the production of energystore+
The energystore+ product range is using Neopor® BMB from BASF, which is manufactured by replacing fossil feedstock with an equivalent amount of renewable resources at the very beginning of the value chain. This kind of production saves fossil resources and further improves the positive sustainability profile of EPS. The use of renewable raw materials significantly reduces the product carbon footprint of Neopor® BMB compared to traditionally produced Neopor®. The attribution of the renewable share of feedstock according to a mass balance approach is independently certified by REDcert².
“We’ve worked closely with energystore for many years”, says Phil Marsh, Commercial Manager UK & Ireland for Styrenic Polymers at BASF. “We’re delighted that energystore is the first UK company using Neopor® BMB for high-quality insulation solutions. It is of utmost importance for us to contribute with our products to reducing fossil resources consumption and greenhouse gas emissions during our production as well as reducing greenhouse gas emissions generated by heating or cooling buildings.”
The first project using energystore TLA+ was successfully installed in a major London renovation project in February 2023.
You can find out more about Sustainability at BASF here.
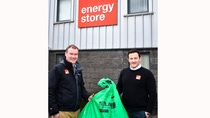
Neil Ferguson, Technical Director energystore, (left) and Connor McCandless, Group Sales & Innovation Director energystore (right)
Commercial enquiries should be directed to Phil Marsh, Commercial Management UK & Ireland, Phone: +44 777 0447613 or email: phil.marsh@basf.com
For media enquiries or to repurpose this article, please contact Emma Gregory at emma.gregory@basf.com