The BASF House
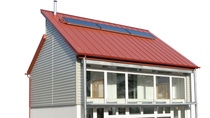
We built this eco-efficient house to demonstrate how the right thermal materials can provide affordable and low carbon solutions for buildings.
The BASF house, which opened in January 2008, is part of the University of Nottingham’s Creative Energy Homes project. In its design and construction, we used low energy principles from the PassivHaus Standard.
Creative Energy Homes
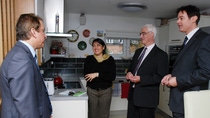
The Creative Energy Homes project showcases energy efficient homes of the future. It aims to stimulate sustainable design ideas and promote new ways of providing affordable, environmentally sustainable houses.
The seven-house development provides a living test-site for leading firms to work with the University to investigate the integration of energy efficient technologies into houses.
The project attracts over 3000 visitors every year, including a Chancellor of the Exchequer, Climate and Housing Ministers, MPs, Vice Chancellors, Industry, Government Departments, Schools and Colleges. Research findings have been fed into the UK government’s Green Deal strategy and the Nottingham Community Climate Change Strategy.
Energy Efficiency and Monitoring
We selected high levels of insulation to minimise fabric and infiltration losses. This achieved a U-value of 0.15 for the walls and roof. We used a combination of insulation materials to demonstrate the range of insulation materials available to produce low energy buildings. All materials were responsibly sourced to ensure lower environmental impact over their life cycle.
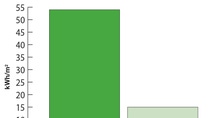
Since its completion in 2008 the house has been occupied by both University staff and students and has been carefully monitored to provide the University of Nottingham, BASF and industry with vital data on the advantages and disadvantages of living in an airtight, highly insulated structure.
Data from the building’s sophisticated monitoring equipment indicated that the house was exceeding the predicted energy target of 15 kWh/m2 and achieving results of 10 kWh/m2.
Living in The BASF House
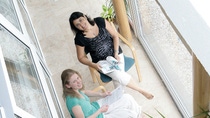
During a year long research project, two PhD students at the University of Nottingham lived in and studied the BASF House. Nina Hormazábal Poblete and Deborah Adkins evaluated the energy efficient designs, construction techniques and technologies used to build and equip the house.
Nina, 43, an Assistant Professor at the University Technica Federico Santa Maria in Valparaiso, Chile, was in Nottingham doing a PhD on Post Occupancy Evaluation, specifically for low energy homes. Deborah, 27, lived in the house during the third year of her PhD studying sustainable energy technologies.
Data from the building’s sophisticated monitoring equipment helped them to evaluate energy consumption and a range of climatic conditions in the house from the temperature and relative humidity to the lighting, solar radiation and ventilation.
An important aspect of the Post Occupancy Evaluation was the general comfort of the house and its affects on the occupants. Nina and Deborah were electronically tagged while in the house to create a record of their living patterns.
Their initial reactions were mainly positive. They found the house very light and airy and described the natural ventilation as fantastic for such a relatively small house. They said the high ceilings really helped and the sunspace made the house feel bigger.

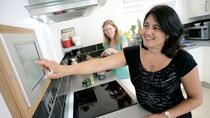
The Design
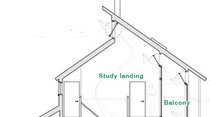
The two most significant aspects of the brief given to Derek Trowell Architects made the house different in appearance from more conventional housing. The house was to be extremely energy efficient, with as near as possible zero carbon emissions, and it was to be extremely economical and affordable.
The environmental design strategy, proposed by the University of Nottingham’s Built Environment team, combined natural ventilation with a high thermal capacitance interior. This helps to avoid overheating. Active cooling is not needed because of south facing glazing and controlled natural ventilation. Phase change materials (PCM) encapsulated within plasterboard helped to achieve a high thermal capacitance interior.
The house has a compact floor area and relies as much as possible on passive solar design. The total annual heating load is around 1200Wh which translates into 12.5kWh/m2. The house complies with the Passivhaus standards of 15kWh/m2 and can be called a 1.5 litre house.
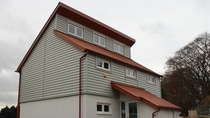
Simple Design
The design is extremely simple. The north, east and west walls are highly insulated, with the minimum number of windows compatible with acceptable daylighting standards. Absence of windows on the east and west sides means that the house can also be built as a terrace or semi detached unit.
North facing windows are double glazed and gas filled, with a U-Value of under 1.7. The top windows are fitted with thermal and rain sensors running on electric motors that enable the passive house ventilation to operate through an innovative and affordable home automation system.
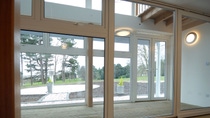
Sunspace
Facing south there is a fully glazed, adjustable two-layer sunspace. The sun warms the air in the sunspace and acts as the house’s primary heating source. Windows between the sunspace and the main part of the house can be opened to enable the warm air to flow around the rest of the house.
The sunspace can be temperature controlled to prevent overheating, using motors on upper windows to vent excess heat. A ground to air heat exchanger brings fresh, pre-warmed air into the solar area. In summer this system also provides cool air directly into the main house.
The design is similar to that used in oast houses for drying hops. The staircase acts like a flue, drawing warm air upwards through the house.
South Elevation:
Inner conservatory (double glazing): 1.7 W/m2 °C
Outer conservatory (single glazing or similar): 2.7 W/m2 °C
Heat Management
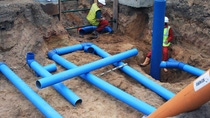
Ground Air Heat Exchanger
REHAU's Awadukt Thermo® ground-air heat exchanger system for controlled ventilation, in combination with heat recovery devices, helps to save money and energy. An anti-microbial inner layer significantly improves air quality in the house.
Fresh air, drawn through an underground network of pipes, is pre-heated in winter or pre-cooled in summer using energy stored in the ground. At a depth of 1.5 metres the ground is a constant 8-12°C.
There is one inlet pipe in the back garden and outlet pipes into the dining room and living room. During cooler months air entering the sunspace is warmed by the sun before it enters the open plan living and dining room areas.
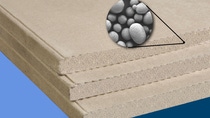
Phase Change Materials
To reduce the cost of energy required to cool the house, we used plaster board incorporating Micronal® PCM. Micronal is made of polymer capsules containing a special wax mixture which stores latent heat.
When the temperature rises over a defined temperature threshold of 23°C, the wax melts and the phase change material absorbs heat. When the temperature drops, the wax solidifies, and heat is emitted.
Micronal contributes to an improved indoor climate, more comfortable living conditions and better energy efficiency.
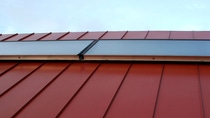
Solar Power
Solar power provides an estimated 81% of the hot water. Hoval’s Soikit® compact system for solar-powered Domestic Hot Water (DHW) generation was combined with solar collectors suitable for all roof types or for wall mounting.
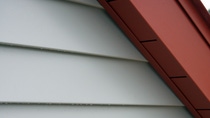
Roofing & Cladding
Colorcoat Urban® by Tata Steel provides a lightweight, durable, waterproof cladding for the first floor and roof.
Traditional roofing materials absorb solar energy, generating heat that is transported by thermal conduction into the roof and by convection to the surrounding air.
Due to the reflective properties of the roof, the BASF House absorbs less solar energy, so less heat is available for release when the temperature drops. This can contribute to reducing any local environmental heat island effect.
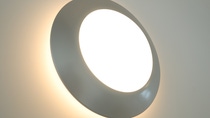
Lighting
The house lighting system, which includes mains power battery backup, maximises the use of low energy, low voltage LED (light emitting diode) lighting technology.
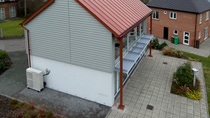
Heating
Panasonic partnered with Cool Planet, the renewable energy design and installation arm of British Gas, to deliver an eco heating solution. Following completion of testing on a biomass boiler, Cool Planet installed a 9 kW Aquarea monobloc unit in spring 2011.
The Aquarea unit, serving the wet radiator system, can raise the water temperature from 27°C (typical overnight standing temperature) up to 43°C (typical acceptable hot water temperature) within 1 hour.
Using air as the energy source, Aquarea can provide fuel bill savings of up to 78% compared to direct electric heating. For every kW of electricity consumed, it returns 4.74 kW of energy, i.e. 3.74 kW more than a conventional electric heating system.
The Construction
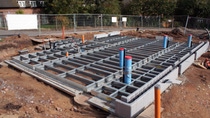
Foundations
Roger Bullivant supplied the sub-structure, using their “System First” Foundation system. They set out the outer perimeter of the steel profile using Neopor® ICF LOGIX blocks, to provide a good foundation for the ICF blocks which form the ground floor walls, and built air pipes for under floor ventilation into the ICF perimeter blocks.
They inserted pre-cut Neopor® insulation into the steel framework and used a hot wire tool to channel out space for the pipes that carry hot water from the solar thermal and biomass systems, so that the water does not freeze during the colder months, before applying a final layer of concrete and filling all the spine sections with reinforced concrete.
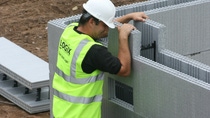
Ground Floor Walls
A team from Logix built the ground floor walls from their ICF (Insulated Concrete Formwork). The ICF system is based on ODPM Zero, lightweight CFC free expanded polystyrene moulded blocks made from BASF’s Neopor®.
These blocks were assembled to create the shape of the building, including window and door openings. The forms remained permanently in place after the core was filled with a pumpable concrete containing a specially formulated BASF concrete admixture. This process took two hours and used about 12.5 m3 concrete. The concrete was allowed to set for the remainder of the week before work started on the downstairs internal walls.
First Floor & Roof
Above ground floor level, we used prefabricated timber Structural Insulated Panels (SIPS) containing Elastopor® rigid polyurethane foam insulation because of their light weight, high insulation factor and the ability to prefabricate non-rectangular shapes, such as gable walls, off-site. The roof was constructed of the same material.
It took less than a day to erect all of the first floor walls. The use of SIPS created a highly insulated and energy efficient, quick to erect building envelope. Benefits include reduced energy consumption, 90% less air leakage than timber stick-framed structures, and no thermal bridging or convection looping.
Materials

Micronal® PCM
To overcome overheating during summer months, we used a modified plasterboard incorporating phase change material, to help regulate the temperature.
Micronal® PCM materials provide an alternative to air conditioning. Microscopically small polymer spheres contain in their core a wax storage medium. When there is a rise in temperature over a defined temperature threshold (21°C, 23°C or 26°C), the wax absorbs the excessive heat energy and stores it in phase change. When the temperature falls under the temperature threshold, the capsule releases this stored heat energy again.
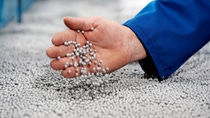
Neopor®
Neopor Is an expandable polystyrene (EPS), an innovative refinement of the classic BASF invention for insulation and packaging, Styropor®.
Foams made of Neopor are grey because they contain graphite, which considerably enhances the insulating capacity. Foam manufacturers can save up to 20% raw material for the same lambda value and installers can work with panels that are 20% lighter in weight or up to 20% thinner.
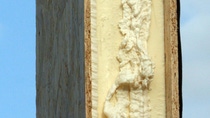
Elastopor® H
Elastopor® H, a closed-cell polyurethane rigid foam, has extremely low thermal conductivity levels and Its insulation properties are very high even when thin. Elastopor H® systems are a significant component of multi-layer construction elements (known as sandwich panels) featuring a polyurethane insulating core and diffusion-resistant metal coatings.
Springvale Platinum EPS
We added an additional layer of Springvale Platinum EPS insulation internally to the SIPs panels and internally and externally to the ICF to ensure a U-Value of 0.15. In the foundations 8 m3 of Springvale Platinum Floorshield EPS 120 high-grade insulation at 120 mm thickness provide high levels of thermal performance. This rigid, lightweight insulation board, with a closed cell structure, incorporates BASF’s Neopor®, enabling it to deliver high insulation values. It is manufactured without the use of CFC’s or HCFC’s, has virtually zero ODP (Ozone Depletion Potential) and zero GWP (Global Warming Potential). Using the BRE environmental profiling system, Platinum scores as few as 0.043 Ecopoints over a 60 year lifespan.
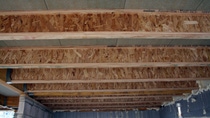
Wolsit® KD20
The softwood timbers used in the house were treated with Wolsit® KD20, a wholly organic wood preservative from BASF Wolman GmbH. The timber was treated in the double-vacuum process, which injects preservative into an envelope of protection around each component and results in service lives of many decades by protecting against attack from xylophagous insects and fungi.
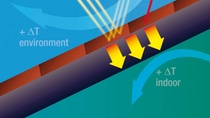
Pigments
When radiated energy from the sun hits a coloured surface the radiation is absorbed. This generates heat, which is transported by thermal conduction into the material and by convection into the surrounding air. Less absorption means less heat build-up.
Innovative pigments from BASF make it possible to formulate surface coatings that significantly reduce the heating effect in sunlight. Reflection from the colour-coated surface contributes to lower temperatures in the coating, lower temperature strain in coating layers and substrate, and a longer lifetime for the coated material.
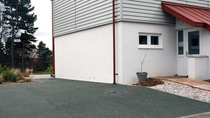
Elastopave®
Around the house we used BASF’s Elastopave®, an elastomeric system for coating gravel that allows water to permeate through the surface into the earth below, enabling valuable water to refill the water table.
Elastopave® polyurethane is a two component polyurethane binder. When combined with local aggregates, it creates a strong, durable composite that can be used for car parks , driveways, footpaths, and patios.