Chinaplas 2023: BASF presents co-creations accelerating the plastics journey towards a more sustainable future
- Co-creations include Net Zero Journey Concept House, concept pillow, electric vehicle charging gun, cable & battery cover
- Partners Landsea & Landleaf, Ebusbar, ShangShang Cable, Gotion, and Guangdong J&Y Industrial for the co-creations
- BASF at Chinaplas 2023: Hall 17; Booth no. 17F71, Shenzhen World Exhibition & Convention Center, China
Shenzhen, China – April 3, 2022 – At Chinaplas 2023, BASF presents co-creations demonstrating its efforts in improving how plastics are made and developing material solutions that increase energy efficiency, extend product shelf life, and enable more sustainable applications in infrastructures for eMobility and renewable energy.
“Together with our customers, we are accelerating the plastics journey towards a more sustainable future. The co-creations also illustrate that collaboration from an early stage of product development, from design to material selection, simulation, and prototyping, helps to speed up time-to-market,” said Andy Postlethwaite, Senior Vice President, Performance Materials Asia Pacific, BASF.
The co-creations revealed at Chinaplas 2023 are:
- Net Zero Journey Concept House - A concept house developed with Landsea and Landleaf: The thermal insulation solutions displayed in the concept house improve energy efficiency, which translates to lower energy bills and a reduced carbon footprint. The insulation materials shown are further fire-safe & EHS-compliant. For instance, the interior wall and flooring made with Elastospray® polyurethane (PU) spray foam provides superior thermal performance and enable space-saving and flexible wall design. The concept house also features renewable energy solutions for wind and solar energy applications. This includes the PU solutions Elastocoat®, Elastan®, and Elastolit®, which reduce carbon emissions and are more sustainable as they can be used indefinitely without depleting natural resources. The exterior flooring is made with BASF’s Elastopave® system for pavements. The high-performance PU incorporates recycled rubber granules for a long-lasting, flexible, and environmentally-friendly solution.
- Electric vehicle charging gun and cable developed with Ebusbar & Shang Shang Cable: The electric vehicle charging gun and cable is designed for supercharging piles using a liquid cooling system to regulate the temperatures of charging components and prevent them from overheating. Liquid cooling systems are generally considered the best option for cooling charging pile cables and guns because of their superior heat dissipation capabilities and less energy use. For the co-creation with Ebusbar and Shang Shang Cable, the housing of the charging gun and cooling pipe of the charging cable are made with Ultramid® polyamide. For the cooling pipe of the charging cable in direct contact with the liquid coolant, Ultramid was selected as the material of choice owing to its exceptional flexibility and chemical resistance. For the housing of the charging gun, Ultramid provides toughness and good aesthetics. The cooling module inside the charging gun is made with Ultramid Advanced N owing to its high heat resistance, dimensional stability, and chemical resistance. The cable sheath is made with Elastollan TPU as the material solution possesses flexibility and long-term durability.
- Spray transfer molding (STM) full plastic battery pack cover developed with Gotion: The PU glass fiber composite technology significantly reduces the battery cover's density and weight. The part has also passed the air tightness test and submersion test. The material possesses superior strength and toughness, providing excellent protection for the battery cover. The STM solution has met the industry flame retardant test UL94 V-0 and GB38031-2020 and is widely recognized as the preferred material for electric vehicles. Further, the solution does not require pre-forming compared to traditional polyurethane composite molding processes. As such, the production process for the spray transfer molding (STM) polyurethane composite battery pack cover is more efficient. It is also a cost-efficient solution for local part manufacturers as the investment of the equipment and molds for new mass production projects is relatively low.
- Concept pillow developed with Guangdong J&Y Industrial: The concept pillow shows how furniture can be made more sustainably. The pillow is made with Freeflex® TPU (thermoplastic polyurethane) 3D mesh, and the cover is made with Freeflex fiber. This is the first time that Freeflex has been applied to pillows. With Freeflex, the pillow is recyclable and a more sustainable material option as primary chemical components can be recycled, making it suitable for environmentally conscious manufacturers. Besides being washable and breathable, its soft touch feeling, body support, and excellent cushioning provide superior comfort. It also inhibits bacterial growth, is easy to clean, and is resistant to ozone for ozone disinfection.
For updates on BASF at Chinaplas 2023, click here or follow our BASF PM WeChat Channel.
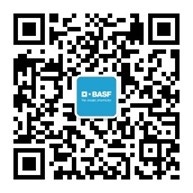
About BASF
At BASF, we create chemistry for a sustainable future. We combine economic success with environmental protection and social responsibility. More than 111,000 employees in the BASF Group contribute to the success of our customers in nearly all sectors and almost every country in the world. Our portfolio comprises six segments: Chemicals, Materials, Industrial Solutions, Surface Technologies, Nutrition & Care and Agricultural Solutions. BASF generated sales of €87.3 billion in 2022. BASF shares are traded on the stock exchange in Frankfurt (BAS) and as American Depositary Receipts (BASFY) in the United States. Further information at www.basf.com.