Change for climate
A green engine for chemistry
Steam crackers are the engines at the heart of the chemical industry. The high-temperature, gas-powered furnaces are essential for basic chemical production, but the process is energy-intensive and emits significant amounts of CO2. To address the climate and energy challenge, BASF, Sabic and Linde started construction of the world’s first demonstration plant for large-scale, electrically heated steam cracking furnaces in 2022. In April 2024 the three companies celebrated the start-up of the demonstration plant. Our goal for this project: Reducing CO2 emissions of one of the most energy-intensive production processes in the chemical industry by at least 90% compared to technologies commonly used today.
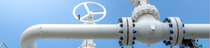
The idea: take the change to heart
Many everyday products are made from materials that wouldn’t exist without steam crackers – furnaces, that typically run at extremely high temperatures of around 850° Celsius. At the start of the chemical value chain, these furnaces break down long-chain hydrocarbons from a raw gasoline called naphtha. The process produces olefins and aromatics – chemicals that are the basis for many products, including vitamins, solvents, specialty chemicals, plastics, and pharmaceuticals.
But, today, the steam cracking process is powered using fossil fuels. Electrification of the furnaces could possibly transform the heart of the global chemical industry.
The basics: Naphtha
Naphtha is distilled from crude oil. It is used for gasoline production, but also forms the basis for ethylene and propylene, benzene, toluene and xylene. Together with methanol and ammonia, they are the seven primary chemicals on which almost all industrial organic chemistry is based.
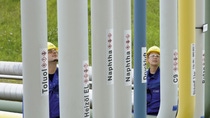
BASF’s Verbund site in Ludwigshafen has its own harbor. From this terminal, primary ingredients for chemical production such as naphtha, methanol or compressed liquefied gases are transported through pipelines directly to the production plants or holding tanks.
The mission: rethink the essentials
BASF has set ambitious goals and is striving worldwide to achieve net zero CO2 emissions1 by 2050. To reach this milestone, the transition of chemical production to renewable energy sources is essential. The eFurnace project could have a major impact on the chemical industry´s journey to climate neutrality. The demonstration plant aims to show that compared to conventional steam crackers, CO2 emissions can be reduced by at least 90%. This goal includes Scope 1, 2 and 3.1 emissions – that includes emissions directly from heating the steam cracker and emissions from steam and electricity.
Learn how we are reducing emissions
More about our climate protection goals
1 The goal includes Scope 1, 2 and 3.1 emissions. Other greenhouse gases are converted into CO2 equivalents according to the Greenhouse Gas Protocol.
The build: integrating the impossible
Construction of the eFurnace demonstration plant started in 2022 and was completed in April 2024. If successful, it will prove that electricity from renewable energy sources can effectively reach the temperatures required to produce basic chemicals. Two heating concepts are being tested in parallel: direct heating, where the electric current is directly supplied to the process pipes inside the reactor, and indirect heating, using radiant heat from heating elements surrounding the pipes.
The prototype will be fully integrated into one of the two existing steam crackers at BASF´s site in Ludwigshafen. BASF also operates steam crackers in Port Arthur (Texas), Antwerp (Belgium), and Nanjing (China).
Watch the video about the final steps at the eFurnace construction site.
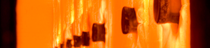
The goal: a pilot for transformation
The eFurnace demonstration plant will process about four tons of hydrocarbons per hour. The plant will use about six megawatts of renewable energy from wind, solar and water power to break down this amount of long carbon chains into olefins and aromatics.
This illustrates the significant energy needed to operate steam crackers and the potential CO2 savings that might be achieved if this pilot project is successful. If all steam crackers worldwide were heated with green electricity, it would have a significant impact on the green energy demand of the chemical industry.
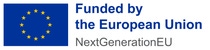
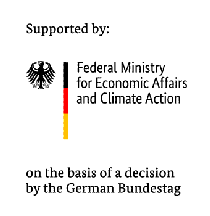
The future of green chemistry: funding for change
The German Federal Ministry of Economic Affairs and Climate Action has recognized the huge potential of the project — the development of the eFurnace demonstration plant is supported with 14.8 million Euro through the “Decarbonization in Industry” funding program, a program assisting energy-intensive industries in Germany in their efforts towards carbon neutrality. The project is funded by the European Union as part of the NextGenerationEU program.
BASF’s mission to achieve Net Zero CO2 emissions and electrification of the hugely energy-intense steam cracker is a significant milestone in our transformation journey.
BASF “Verbund”: efficient use of resources
“Verbund” means “to be connected” in German. At BASF, sustainability is already a living reality. At our unique Verbund sites, production facilities, energy flow, logistics and infrastructure are interconnected in an intelligent way enabling us to use energy and conserve resources more efficiently. By-products from one process are used as raw materials for others. This not only reduces emissions but also lowers logistics costs. Intelligent networking also enables optimal energy supply at our sites. For example, waste heat from the production process in one plant is utilized as energy in other plants.
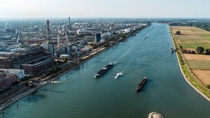
BASF has six Verbund sites worldwide, located in Europe, North America and Asia. They are our main producers, accounting for more than half of BASF’s products. BASF operates 233 other production sites.
Read more about green chemistry at BASF:
Funded by the European Union - NextGenerationEU. The views and opinions expressed are solely those of the author and do not necessarily reflect the views of the European Union or the European Commission. Neither the European Union nor the European Commission can be held responsible for them.