Plastics & Rubber
"Cavus" - Optimal combination of lightweight construction, mass production and cost-effectiveness
Complex hollow parts mass-produced in an automated process at competitive prices – this is now possible with the reactive polyurethane resin Elastolit® R by BASF: The result of the award-winning project of KTM Technologies, H2K Minerals, Teufelberger and BASF can be seen on the K Fair: a mountain bike handlebar implemented as a geometrically complex hollow part with undercuts. The project called “Cavus” takes an integrative view of the process chain – from core formation and the manufacturing of the preform with braided carbon fibers, via the HP-RTM process (high pressure resin transfer molding) using BASF’s reactive polyurethane resin to the dissolving of the core material.
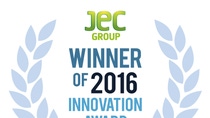
The compact PU reactive resin systems are noted for their extremely broad processing window and are easily demolded with the aid of suitably adapted internal release agents. In addition, they are also compatible with all conceivable process variants (vacuum-assisted RTM, variothermal RTM, gap impregnation, liquid impregnation in the open mold). The BASF simulation tool Ultrasim® helped to find the optimal process management and to reduce the mechanical loading of the core during injection.
Find out more on “Cavus” here and at our booth at the K 2016.