Plastics & Rubber
For modern combustion engines: expanded polyamide portfolio for the charge-air duct
BASF is responding to the development of engine designs in the automotive industry with a consistent portfolio of polyamide 6 and 66 grades that meet the higher demands on the materials. Depending on the base polymer and stabilization system, the plastics are resistant to heat aging up to 220°C and show excellent burst pressure and weld strength.
This means the part developer can be provided with the optimum material for each of the different components in the charge-air duct that offers the best value for money. Selected grades are based on global specifications: They are supplied worldwide from local manufacturing facilities, with uniform material properties and a consistently high level of quality.
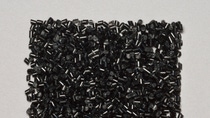
BASF offers polyamides for the various temperature requirements of the charge-air duct. The range comprises PA6, PA66 and PA66/6 grades with a glass fiber content between 30 and 50 percent. Ultramid® B3WG6 GPX, a PA6 containing 30% glass fiber, has been newly added to the portfolio. It is resistant to temperatures up to 180°C and for a short time up to 200°C. Due to its excellent burst pressure and weld strength, it is suitable for air intake manifolds made from several parts. The upper end of the temperature range is covered by Ultramid® Endure, a specialty polyamide which can stand constant use temperatures of 220°C and peaks up to 240°C. For temperatures between 180°C and 210°C, the portfolio contains PA66 plastics with enhanced heat stabilization. These include Ultramid® A3W2G6 to G10 (with glass fiber reinforcements from 30 to 50%) for temperatures up to 190°C, e.g. in charge air cooler endcaps, and the new Ultramid® A3W3G7 for temperatures up to 210°C.
Find out more on Ultramid® in automotive applications here and at our booth at the K 2016.
For further technical questions on the product, please contact the Ultraplaste-Infopoint:
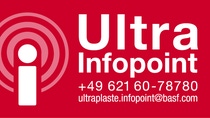