Media
Shaping the future with polyurethanes
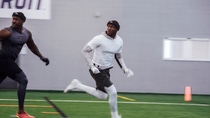
Polymeric materials improve a multitude of applications, make our lives easier, safer, and more comfortable and they can be customized for broad applications. Liying Wang developed a passion for new polymeric materials while she was a Ph.D. student at the Max-Planck-Institute of Colloids and Interfaces in Potsdam, Germany. Since joining BASF in 2011, this passion has driven her to dive deeply in the polyurethane (PU) world. The latest highlight: her project team developed smart PU foams tailored to the specific needs of football players. These smart foams improve the performance of protective gear such as helmets, shoulder pads and masks.
I am a Senior Scientist and work on the development of polyurethane systems at BASF’s Performance Materials division. My research is focused on developing new polyurethane products for various applications, including spray polyurethane elastomers for footwear, reactive polyurethane for 3D printing sneakers, elastomeric viscoelastic foam for sport protective equipment, acoustic and non-flammable flexible foam for engine cover, and lightweight reinforced PU composites for structural panels. I am convinced that polyurethanes can be the answer for almost any kind of application.
Xenith, an athletic equipment company, sought to create the protective headgear for non-tackle football. They reached out to us for a joint project targeting new material solutions. Unlike commercial open-cell PU foams for impact absorption, the new material we created for Xenith, Kinetix foam, has a microcellular structure and features unique characteristics of viscoelastic, elastomeric and lightweight. Upon impact, the foam stiffens dynamically from surface to core and absorbs energy across the full spectrum of impacts. Kinetix foam was designed to be soft and the softness or hardness is adjustable to personalization. So, in addition to protection from impacts, it offers all-game comfort.
The impact absorbing characteristics of Kinetix foam can also be customized by material properties and provides greater flexibilities in Xenith’s new product design. Xenith and BASF are currently working on next generation Kinetix foam for comfort padding for tackle football helmets.
Polyurethane is one of the most versatile polymers in material science and its applications are limitless. While working on various customer projects over the years, I realized that my expertise and knowledge acquired in polyurethane fields are expanded and transformed to a whole new level when I implemented them to solve technical challenges or shared them with others. It is a fascinating experience!
Polyurethane is hands-on science. Besides acquiring PU knowledge from books , you gain expertise by actually using it in the lab and on production machinery. From formulation development to product commercialization, it’s a great feeling to see customers being so excited and successful with our developments.
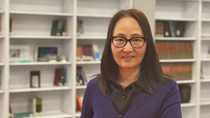
The mastermind behind BASF's PU innovations: Senior Scientist Liying Wang
For media inquiries and questions, please contact: katharina.meischen@basf.com.