Media
Pushing the green envelope: Samantha Gee
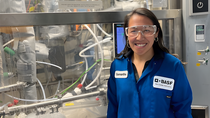
Her love of math and science naturally led Samantha to follow in her father’s footsteps and study chemical engineering. After completing her Ph.D. at Georgia Tech, she joined BASF’s Leadership Development Program (LDP), and after three rotations, she settled in Houston and became a member of the North America Chemical and Process Engineering group.
Today, she is in charge of the new sustainability pillar inside the group, steering new and innovative solutions to implement them successfully across BASF’s value chain.
What exactly does the Chemical and Process Engineering Group do?
We're a centralized process research group. We support our North American sites, and we support various BASF operating divisions (ODs). We have expertise in process optimization, equipment design, troubleshooting and plant support.
We actually have five pillars within the group: fluids process engineering, reaction engineering, solids processing, Computational Fluid Dynamics (CFD) simulations and safety engineering. Now, we are adding a sixth pillar, sustainability, because it is something we feel is a core value and there's enough demand from the ODs to take it on.
Our group ethos is: “Help will always be given by our group to those who ask for it”, sort of echoing Albus Dumbledore from Harry Potter.
ODs come to us when they have challenges or are experiencing issues so that we can evaluate the different processes and see if we can improve them; and now they also come to see if we can make those processes more sustainable.
Our group is approximately 30 people, and we work on over 150 projects per year. So there are quite a few projects. They typically save BASF €8 to €10 million per year, and I was involved in some of these projects.
For example, we had a project at our site in Beaumont, Texas, where we wanted to improve the yield of the reaction, but the reaction was limited because it was not properly mixed. So, we examined if we could improve the mixing of the product by changing the angle of the impeller blade and the location of the gas feed. Ultimately, we achieved a 2 to 3% yield improvement, which can translate to nearly a million euros saved per year.
Tell me about your new position as sustainability lead.
I was part of the reaction engineering team, which was a fantastic experience, and it gave me a good foundation for a lot of the things we do today. However, over the past few years, there's been increased demand and attention within BASF for becoming more sustainable by measurably reducing our emissions and lowering our product carbon footprint in line with our aspirations. With several targets set for us such as reducing CO2 emissions by 25% by 2030, this area of driving sustainability feels super charged!
As lead of the sustainability team, I am still very focused on supporting our ODs, but with the goal of improving the sustainability of our processes.
For example, every product has a product carbon footprint. A certain amount of CO2 gets produced for every product. What we're seeing right now is that there is a huge demand from our customers to reduce the amount of CO2 per product. By understanding the mass balance approach, the energy requirements, and the raw materials that go into our processes, we can see the impact that we would have on that product’s carbon footprint.
It's really about understanding the process and seeing if there are alternatives that we can adopt. We evaluate various transformative technologies, but we also look into how we can improve our existing processes. Maybe we can use a different solvent or use a different catalyst. Maybe we could feed both bio-based and petroleum-based material together to then increase the bio-content overall. It's going to take a lot of steps to get there. But that is our objective.
What are the challenges the sustainability team is facing today?
The main challenge is you screen different technologies, methods, etc. Something might be good theoretically, but it might not work when it gets implemented at scale. Trying to determine what is actually technology-ready and what is getting hyped is essential. Many ideas are attractive, but they also have to align with BASF’s value chain.
But I think the biggest thing is evaluating whether we should take the risk or not. Chemical and oil companies are going through a huge industry transformation in general. If a company is going to be a leader and entrepreneurial, there’s going to be a level of execution risk. There are always going to be followers too, who see if it's been implemented and how it goes first before adopting it.
But if a company waits and is a follower, it will always pay a premium in terms of cost. For example, when it comes to using bio-based feedstocks, the favorable ones already have long-term contracts with limited availability.
How has this role affected your relationship with academia?
I used to work a lot with our ODs, especially in operations. That was the focus, whereas now I work a lot with external partners as well, such as national labs and academia. There are some things that we want to work on that just need more development and are higher risk and sometimes we don’t have the necessary expertise at BASF.
There's been a lot of push from the U.S. government to fund sustainability-based projects. They always have a call for proposals, and we actually have won several of them with our BASF colleagues and academic partners. Many of these ideas or projects have been studied at the academic and national lab levels, so it's great to be working with them and getting those initial results and expertise.
Having industry partners from the very beginning, even if it's from a consulting perspective, can really make a difference. By collaborating with academic partners early on, we can leverage the data from their experiments and work together to obtain applicable and scalable results. The jump to implementing a solution at the industry level takes a lot of work. For instance, if there's a bit of impurity in an academic study, it's not considered a big deal. But for us, that bit of impurity gets amplified considerably when it's at a bigger scale and we not only have to spend a lot of money making these chemicals, but also purifying them, and that can be just as consuming.
We all bring something different to the table. Our academic partners have quite a bit of expertise in research and can go into the details of really understanding it. But what we are bringing is the way to implement it.
What are you hoping to achieve with this new role?
As we look at our society and see how we're living right now, we know we can't continue this way. We have to work on these sustainability-focused projects. It all ties back to the work we’re doing. These process improvements and these massive energy and industry transformations are going to take years to overhaul and implement.
The most attractive part of this industry is that every product made is going to touch society in some way. That drives a lot of people, but especially me. I was shocked, and I think most people are, about the number of products that BASF makes and how mostly everything people use in their daily lives is somehow connected to our company and our chemistry. So I always want to see the impact of the work I do.
We don't have time to wait. My child and other people's children are going to benefit from the decisions we make today. For me, it means trying to make sure that we leave them a better place.
For questions, please contact mariana.licio@basf.com
For media inquiries, please contact molly.birman@basf.com