Stay with the wind
Why can plastic utility poles stand firm and erect in strong typhoon? Besides plastic utility poles, where else can polyurethane composites be applied to?
This July, the formidable 14-force typhoon Rammasun ravaged Guangdong. More than 70,000 concrete and metal utility poles collapsed in the powerful typhoon, which not only resulted in heavy property loss, but also brought power failure to large tracts of areas. Nevertheless, what’s surprising is that throughout the typhoon attack, a group of plastic utility poles stood firm, and merely “sway with the wind” amid the gusts of typhoon.
Of course, the plastic utility poles resistant to typhoon do not use common plastics. Instead, it uses a kind of high-strength and high-flexibility polyurethane (PU) composite material developed by BASF. Compared with the common utility poles, this kind of new utility pole made of Elastolit®, a BASF PU composite material, can improve its wind resistance by 2.5 folds.
What’s more, because the new plastic utility pole is a hollow cylinder, its weight is only less than a quarter of the same type concrete utility pole – the weight of a common concrete utility pole is generally 1,100 kilograms, whereas that of a plastic utility pole is only 250 kilograms, making it possible to be carried and installed by manpower. In terms of installation spacing, this kind of lightweight PU composite utility pole can extend the installation spacing to 120 meters, whereas that of common utility poles is 50 meters at most.
The secret of “no falling” of the utility poles lies in the innovation of the new material. Traditional utility pole mainly relies on its own weight to take root in the ground, so as to gain support. However, when encountering ultra-large typhoons, such pure “rigidity” will lose resistance. On the contrary, only utility pole with both “rigidity” and “flexibility” can stand firm in the more powerful typhoon. Combining both qualities, the new plastic utility poles are exactly a compound of glass fiber and PU through filament winding technique.
“BASF’s inspiration for re-innovate utility pole came from the local market needs. This is an innovation born in the R&D labs in Shanghai,” said Dr. Han Wei, Senior Manager of Performance Material Asia Pacific, BASF. “Another important factor is that our global R&D departments have accumulated rich experience in the compounding of glass fiber and PU material.”
PU is a kind of versatile polymer material. It’s lightweight and with wide range of adjustment – meaning it can be either made very hard or very soft. Two objects with seemingly drastically different surface features are very likely the same PU product in essence. Glass fiber features high level of strength, but if there’s no resin-type adhesive to bond them together, it will be like a brittle nylon string and fail to bring out its strength.
After compounding glass fiber and PU, the resulting material can integrate the innate features of both substances thus perfectly combine strength and flexibility. “In fact, the new material is not only strong and flexible, its impact resistance, corrosion resistance and UV resistance are also very good,” said Han. At BASF, glass fiber PU composite has been used in extensive applications. For instance, it replaces metal as the lightweight alternative for exterior decorative parts of automotive.
“There are a number of ways to compound glass fiber and PU. In the case of utility pole, we adopted filament winding process which enables glass fiber to compound with PU as continuous fiber, so as to reach higher strength, but the technological challenge is also daunting,” said Dr. Qian Zhenyu, Manager of Technology R&D Center, BASF.
The biggest technological challenge lies in controlling the reaction time between PU and glass fiber. PU is a kind of material with fast reaction and thus allows short reaction time which is only less than 20 minutes. During such short period of time, it’s challenging for both substances to fully immerse along the winding process. “The R&D team in Shanghai has been working to prolong the operating time of PU, while strengthening its hydrophobic property – it generates bubbles if affected by the humidity of air during long exposure, which will greatly impact the product strength and appearance,” Qian explained.
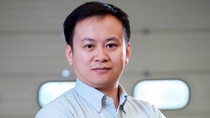
“This is an innovation born in the R&D labs in Shanghai.”
Dr. Han Wei, Senior Manager of Performance Material Asia Pacific, BASF
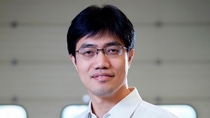
“There are a number of ways to compound glass fiber and PU. In the case of utility pole, we adopted filament winding process.”
Dr. Qian Zhenyu, Manager of Technology R&D Center, BASF
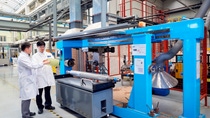
In terms of unit cost, glass fiber and PU composite utility pole is indeed more expensive than the traditional concrete utility pole. “Nevertheless, we should not only appraise the value by the individual product. Instead, the entire lifecycle shall be considered,” said Dr. Karl Rudolf Kurtz, Senior Vice President and Asia Pacific Research Representative, BASF, who is very excited about this innovation created in China.
If taking into account the reduced transportation logistics cost, less installation and maintenance costs, the reduction in quantity brought by extension of installation spacing, as well as prevention of losses resulted from collapses and rebuilding, PU utility pole is not expensive at all. “PU composite utility pole has very high economic value for regions with unique geographical surroundings and meteorological environment, for instance, mountainous regions and sea islands with inconvenient transport access, as well as regions with frequent typhoon attacks,” Kurtz emphasized.
In China’s coastal regions, up till now this lightweight and convenient PU utility pole has been put into market trial. Customers of Southeast Asian regions where there are frequent typhoon attacks also showed intense interest in this plastic utility pole.
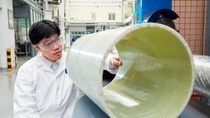
Aside from plastic utility poles, PU composite also has many other application fields yet to be developed. Overall speaking, lightweight is a big trend of industrial products. For instance, for Liquefied Natural Gas (LNG) steel bottle, if a layer of PU composite is coated on the exterior of steel inner container, it can both improve the strength and greatly reduce the weight of steel bottle previously made of pure metal. In another instance, plastic window frame made of glass fiber and PU composite can both reduce weight and obtain far better insulation and energy saving effects than window frame made of metal.
“We are also researching and developing how to apply PU and other composite materials in wind energy, for example the application in wind turbine blade. Blades made of PU composite can extend the service life of existing materials,” Kurtz disclosed. He considers that in shipbuilding and automobile sectors, the potential of composite materials have not been fully tapped. “Each kind of material has its own features. It’s not fair to simply say which is better, yet we must apply their special features to the most suitable applications. The compounding method can also help us create new material features by maximizing the favorable factors and minimizing the unfavorable ones.”
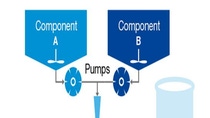
It is exactly for this reason that Dr. Kurtz considers open innovation combining local market insights and BASF know- how is extremely important. “You cannot take hair care products in the European market directly to the Asian market to sell, because Europeans and Asians differ in hair property. Similarly, in Germany the market for plastic utility poles may be weaker than that in China, for there is no typhoon at all in Germany,” said Kurtz.
As an innovator of advanced materials, BASF is joining hands with local partners for more open innovations. “Our innovation is driven by the market needs. Closer collaboration with our customers enables us to creative more valuable solutions,” said Kurtz.