World’s lightweight future
From vehicles to rotor blades, from construction to home furnishings…the trend to “lightweighting”, necessitated by the need for energy efficiency and environmental protection, is now everywhere in our lives.
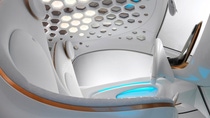
Though it looks like an exquisite toy, smart forvision is no-kidding matter, rather it is a forward- looking electric concept vehicle jointly developed by BASF and Daimler, one of the world’s most successful automotive companies. smart forvision successfully combines the brisk style of smart with a high percentage of plastics in wheels, doors, exteriors, interiors and other components. The result is a 30% weight reduction compared with models of the same level.
“The lightweighting trend is obvious,” said Dr. Piyada Charoensirisomboon, Vice President Innovation Campus Asia Pacific (Shanghai), BASF. “This is especially true in the transportation industry.” In June, the European Union (EU) agreed to a compromise deal to enforce stricter rules on carbon dioxide emissions for all new EU automobiles from 2020, aiming to ensure an average of 95 grams of CO2 per kilometer. However, statistics show that by the end of 2011 German-made cars still emitted more than 143 grams of CO2 per kilometer on average. “Lightweighting is a must to realize this emission reduction goal,” Charoensirisomboon said. It’s estimated that, on average, a weight reduction of 100 kilograms reduces CO2 emission by 10 grams per kilometer. The trend to lightweight can now be found everywhere in our lives.
People want lighter clothes, lighter computers and lighter mobile phones, among other things. Home furnishings needing frequent movement are becoming lighter. “As for transportation, the lighter planes, cars, trains and yachts are, the less energy they consume. It’s no doubt that people favor lighter things, but with one condition – that their performance and safety are not negatively affected,” said Dr. Ates Erk, Head of China Technical Research & Development Center, Polyurethane Specialties, BASF.
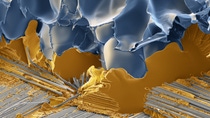
Innovations in lightweight materials provide the basis for lightweighting. To many people, plastics can only be used for decorative or non-important purposes in daily life. Nevertheless, BASF’s innovations in materials are changing this kind of view: plastics are finding their way to replace steel.
“In the automotive sector, plastics are evolving from non-load-bearing decorative components to high-strength functional and structural components that require excellent resistance to impact and heat,” said Michael Sun, Senior Manager specializing in Automotive Market Development for Engineering Plastics Greater China, BASF.
Currently, many lightweight plastic automotive parts and components, including engine covers, front-end modules, lower bumper stiffeners, transmission cross-members, turbo charged engine pipelines, oil pans and body structural inserts, have been commercialized. In addition, the doors of smart forvision are made of carbon-fiber-reinforced epoxy resin. Thanks to their unique advantages, BASF’s lightweight solutions are now benefiting the transportation sector, including high-speed railway and yachting.
“In the automotive sector, plastics are evolving from non-load-bearing decorative components to high-strength functional and structural components that require excellent resistance to impact and heat.”
Michael Sun, Senior Manager specializing in Automotive Market Development for Engineering Plastics Greater China, BASF
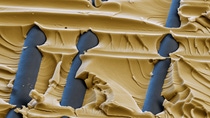
The plastic wheels on smart forvision, however, provide an even better demonstration of the ultimate performance of engineering plastics. The whole wheel, except for an insert connecting to the axle, is made of plastic composites, resulting in a weight reduction of three kilos per wheel. Considering the hundreds of kilos of heavy load and the continuous rotation in driving, it’s easy to imagine how great the challenges are. “While the breakthrough of battery technologies for electric vehicles (EV) seems impossible in the near future, lightweighting becomes the obvious choice to promote the development of EV,” Sun noted. “The lightweight, plastic wheels mark an exciting milestone. It may take a few more steps for all-plastic wheels to be commercialized and our experts are striving to improve their impact and fatigue resistance.”
Compared to plastic vehicles, the all-plastic e-bicycle presented by BASF on K 2013 in October may be closer to commercialization. The “Concept 1865 – Rethinking Materials” e-bike utilized 24 different BASF plastics, including polyurethane composite, thermoset epoxy resin and performance foam plastic to build wheels, body and wires. The BASF plastic body and chassis offered up to a 60% weight reduction potential compared to their steel counterparts. Thanks to lightweighting, the dream of a “portable” bicycle may come true in the near future.
In addition to transportation, lightweighting also has an important role to play in the clean energy sector. BASF, for instance, has successfully applied lightweight solutions in the manufacturing of rotor blades. Lighter blades help capture more wind resources. However, they must withstand extreme conditions, including strong wind load, air scouring, sand impact and UV exposure. In the photovoltaic (PV) sector, the BASF PV module installation frame was not only much lighter than its metal counterpart but also withstood a wind pressure of 2,400 Pa, extending the life service to over 20 years.
Many people may currently doubt the safety and durability of plastics when they are used to replace metals in daily life, but it’s a view that undoubtedly will change with the new technologies available. “Now the application of plastics is not limited to jugs and mugs. To be more precisely, they are composites with higher specific strength than steel,” added Sun, hoping to eliminate people’s prejudices against “plastics”.
Tough and durable as steel, such “plastics” are in fact new materials combining various kinds of glass fiber, carbon fiber and metal power, which presents an important breakthrough for the modern scientific world. The composition and innovation in materials are extremely challenging and BASF research and development (R&D) teams are continually working in this field.
The design and process, however, are critical to ensure plastics parts have similar performance with metal rivals. “Material design principles are subject to specific applications demanding different properties, besides material performance differs according to the processes and methods of production,” Sun noted. “Currently, metal designer are still the mainstream and plastic designers the minority, which is why BASF, as a material supplier, is involved in the product and process design of our customers.”
“In the future, we will settle more and more key R&D competencies in the region to meet the needs of our customers with innovative products.”
Dr. Ates Erk, Head of China Technical Research and Development Center, Polyurethane Specialties, BASF
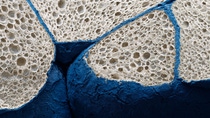
According to Erk, plastics can actually be “very smart” due to their versatility. “People are inclined to consider metal solutions as the strongest and safest ones. Nevertheless, lightweight plastics and composites, with special structural design, can effectively reduce and absorb impact energy and provide increased protection to passengers,” he explained. “Energy absorbing polyurethane foam is just one example of how plastics contribute to car safety.”
Sun emphasized all innovative material parts are subject to stringent safety tests before their commercialization. “Computer- aided simulation systems are very helpful in lowering the complexity and improving testing efficiency. However, currently they still cannot replace the final real-world tests, which ensure absolute safety of the parts,” Sun said.
“The importance of China as market for plastics and composites is growing fast and we already have a strong R&D team in Asia,” added Erk. “In the future, we will settle more and more key R&D competencies in the region to meet the needs of our customers with innovative products.”
“Innovation will require more and more interdisciplinary approach, where experts in different area, industries to find sustainable solution to meet future challenges.”
Dr. Piyada Charoensirisomboon, Vice President Innovation Campus Asia Pacific (Shanghai), BASF
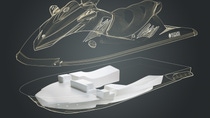
Aspiration for a “portable” life and acceptance of energy-efficient and environmental- protection concepts are among the key drivers for lightweighting. This concept not only makes things conveniently “portable,” but also remarkably reduces energy consumption.
“When people talk about environmentally- friendly materials, the first thing to come up is ‘recycling’. However, BASF takes a whole-life- cycle approach to materials, which consists of four stages from raw material production, parts production, product usage to end-of-life disposal. Recycling is only a small part of it,” Sun said. “Take vehicles as an example, statistics show that product usage accounts for 85% of energy consumption in the whole lifecycle, while in sharp contrast, recycling – even in an ideal scenario of 100% recyclable – accounts for only 0.2%. Therefore, reducing the energy consumption in transportation with lightweight solutions is vital. Of course, our composite materials are actually recyclable.”
According to Charoensirisomboon: “Innovation will require more and more interdisciplinary approach, where experts in different area, industries to find sustainable solution to meet future challenges.”