Extraordinary engineering: building a modular plant in China
Building a Lego house of their own design might be one of the most cherished childhood memories for many people, but can you imagine a real-world chemical plant fabricated like Lego pieces?
In September 2018, a new antioxidant plant achieved its mechanical completion at the BASF Caojing site in Shanghai. Compared to the past, it took only 10 months from approval by the board to completion. During construction, dust emissions were reduced to almost zero and noise minimalized. This was achieved by a high pre-fabrication rate of up to 90%. The plant was divided into 10 modules, each of which was pre-fabricated with devices, pipelines, instruments and cables in the steel frameworks at an offsite workshop. The completed modules were transferred to the construction site, connected to utilities and assembled together.
This is the first BASF chemical plant constructed in a modular way. In a world that demands engineering safety and efficiency, the modularization concept provides a more efficient alternative to onsite construction for BASF large capital projects.
Clear advantages of modular construction
Luce Lu, senior manager of Engineering and Maintenance, BASF Asia Pacific, was responsible for the design, construction and commissioning support of the new plant. He explained that modular construction offers a mix of benefits, from a shortened construction schedule and higher efficiency to more controllable quality and increased construction safety.
Modular construction can significantly reduce the construction period , a stunning speed never achieved before by similar BASF plants. Traditionally, civil construction has to be completed before the laying of pipelines starts; now they can proceed in parallel as modules are prefabricated in different workshop, thus saving time.
Secondly, all fabrication work is completed indoors. As a result, it is unaffected by external factors such as climate and environmental conditions, which not only improves worker productivity but also engineering quality. With welding, for example, the average daily capacity of a worker is about 20-25 dia-inches outdoors, while in an indoor workshop this figure can be increased to 50-60 dia-inches. This is because an outdoor welding operation might have to be paused on rainy days, while a workshop is shielded from external disruptions. Temperature and humidity control, meanwhile, also contribute to better welding quality.
Last but not the least, prefabrication improves construction safety by eliminating potential hazards and pollution. “Fixed scaffolds are commonly used in traditional construction. Workers lacking safety awareness may be exposed to potential hazards as they climb up and down,” said Lu. “In contrast, the 30-meter-high facility fabricated in the workshop completely avoids the need for fixed scaffolds. Only mobile ones are used when needed.” Automated pipeline welding in the workshop not only reduces fumes and noise, but also allows iron filings from machine tools to be recycled.
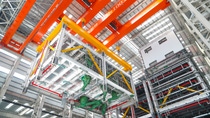
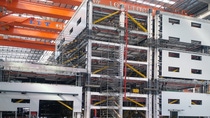
As a result, the pre-fabrication approach was immediately endorsed by the business division for its remarkable advantages. “By building the new plant more efficiently, we shorten products’ time to market and ensure reliability in supply,” said Kin Yung, antioxidant plant operation manager for BASF Chemicals Co., Ltd.
Overcoming challenges
Despite the benefits of this kind of construction, building a modular plant isn’t easy. “At this stage, modular construction involves a lot of limitations – particularly when it comes to the ‘last-mile’ of road transport for prefabricated modules,” said Lu. “As this is BASF’s first-ever modular project in the world, we had no previous experience to refer. We had to start from scratch.” He believes that teamwork among all parties, from engineering, fabrication and onsite construction, has been the key to the project’s success.
Yan Dongbo, Engineering and Maintenance, BASF Asia Pacific, was responsible for the engineering design management on the project. He explained that at the engineering design stage, BASF and the Shanghai office of WorleyParsons, BASF’s global engineering partner, assembled a project team of more than 70 personnel, including nearly 20 core members. “Everyone was involved - including our engineering partner, module manufacturer, equipment suppliers, oversea experts and BASF staff responsible for engineering, technology, operations and maintenance,” said Yan. “Each of the engineers drew on their own areas of expertise to provide precise calculations and designs for each module.”
Given the unique requirements of a modular plant, field investigations were conducted in advance, including the docks en route, cranes, and road conditions during the “last mile” to the Caojing site. Numerous external factors for manufacturing, transport and assembly were taken into consideration before the design work actually began. “When we are designing, we have to consider both the plant itself and the division of modules,” said Yan. “The main unit can’t be split, each module should be easy to transport, and the number of connections between modules must be minimized.”
The most difficult part is preventing any deformation of modules during transport. “Deformation caused by lifting and transport will not only lead to assembly failure but also damage the floor,” said Yan, “To ensure successful assembly, any deviation larger than three millimeters must be avoided.”
The structural designers were confronted with a particularly tough challenge: they needed to fully calculate the module’s stress conditions and find the exact center of gravity to accurately design the connection between the module and the steel structure. To this end, the structural design team collected massive volumes of data, including component specifications and accurate weight on equipment, bridges, pipes, control cabinets, even nuts and bolts, and carried out a huge amount of calculations – three to four times more than in the past – to ensure that each module could be smoothly assembled.
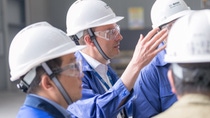
Once the design was completed, the pre-fabrication of the modular plant was initiated in the module yard of LBT Group in Zhangjiagang, Jiangsu province. A renowned modular component manufacturer in China, LBT, with its state-of-the-art equipment and experienced staff, has provided reliable services in a number of overseas projects. Because of the safely-controlled environment of its workshop, the project team could better manage both the safety and quality of the fabrication and achieve zero lost time injury. “In addition, during the pre-fabrication, we were already able to conduct trouble-shooting and make adjustments before commissioning,” said Lu.
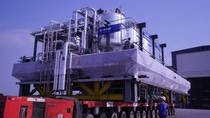
The 24-hour sea and road transport was another critical test of the modular structure.
One of its biggest challenges was safety issues during lifting. “The requirements of the chemical process had left certain modules with a very skewed center of gravity, making them liable to deformation during lifting. Worse still, they could tip the crane over,” said Lu. “Adding counterweights to the crane would solve the problem, but it would also lead to soaring costs. As such, it was necessary to customize lifting schemes for each module’s center of gravity. Assisted by Wang Changyin, a senior manager of BASF who has extensive experience in heavy equipment lifting, and safety assessment experts from the Academy of Safety Engineering, the team designed a more suitable spreader for those modules to ensure the crane’s load didn’t change, it was able to lift each module safely, and the modules themselves weren’t deformed.
This multi-faceted cooperation ultimately yielded gratifying results: almost none of the modules were deformed after reaching the site. Five days later, the plant was assembled and everything had been bolted together perfectly.
Enormous Future Potential
The Caojing antioxidant plant was independently designed and constructed by BASF’s China team and is the company’s first modular project worldwide. The team’s accomplishments are not only a testament to BASF’s integrated capabilities in technology and engineering, but also showcase their technical expertise and value when it comes to quality, innovation, and safety.
“We are honored to be pioneers in pushing forward modularization, which truly enables a fit-for-purpose plant,” said Lu. Yan also said he felt extremely proud when the designs became a reality and everything was fitted together smoothly.
Following the project’s completion, BASF teams from all over the world showed a strong interest in the project and its modularization concept. Large numbers of visitors came to the plant, including engineering colleagues, as well as those from business and technical procurement units. They were eager to learn the various details such as engineering design, communication within the team and cost control.
Lu believes that, as an emerging construction method, the modular approach has enormous potential for the future. “Modular construction could be an ideal option for the areas with higher labor costs or an extreme climate, or chemical plants requiring a high level of standardization.”
At present, the new plant has been constructed as planned and trial production is under way. The products will be launched in 2019 following customer certification. This plant, with an annual capacity of 42,000 ton antioxidants and associated forms and blends, will supplement the current capacity to meet the increasing demands of the Asian market.