BASF in Greater China 2023
Business Development
In 2023, BASF posted sales of approximately €9.4 billion to customers in Greater China. We are committed to being close to our customers and growing together with them. To date, BASF has invested more than €10 billion in Greater China (approximately €14 billion with partners) to build a locally competitive production, marketing, sales, technical service, and innovation network. Our investments enable us to serve our local customers’ needs with sustainable and innovative products and solutions.
Strategic investments in Greater China
- Expanded downstream chemical plants of BASF-YPC
- Zhanjiang Verbund site: inaugurated the TPU plant and broke ground on the construction of several downstream plants
- Enhanced investments in polymer dispersions, anode binder and UVA filters productions
To respond to growing demand from various industries in the Chinese market, BASF is strategically expanding its local production, including sites construction and sustainable development projects.
In Nanjing, the further expansion project of the Verbund site operated by BASF-YPC Co., Ltd. (BASF-YPC), a 50-50 joint venture of BASF and SINOPEC, was completed in November 2023. The expanded plants include a new tert-butyl acrylate (TBA) plant, the first implementation of this advanced production technology outside Germany. The new facilities, powered by renewable electricity, will further reduce carbon emissions during production and provide sustainable products and solutions to the market.
The BASF Zhanjiang Verbund site, with an investment of around €10 billion, is being constructed in several phases and is progressing steadily as scheduled. In 2023, BASF broke ground on an acrylic acid complex, a neopentyl glycol plant, a citral plant, a polyethylene (PE) plant and a syngas plant. These world-scale facilities, fully integrated into the Zhanjiang Verbund site, are scheduled to start up in the next two years.
In January 2024, BASF celebrated the inauguration of its Thermoplastic Polyurethane (TPU) plant at the Zhanjiang Verbund site, which is the company’s largest single TPU production line globally. Built with advanced technologies, this new TPU plant will enhance BASF's capability to satisfy the escalating market demand for TPU in the Asia Pacific region, specifically in Industrial, e-Mobility and new energy segments.
BASF further expanded its production plants to support electric vehicle growth. Two production plants in Jiangsu and Guangdong provinces were modified to produce a wide range of highperformance Licity® and Basonal Power® anode binders for lithium-ion batteries. Modifications enabled a capacity of more than 100,000 metric tons per year to support a stable supply of anode binders from mid-2023 onwards.
To serve the fast-growing architectural coatings, construction, and battery binder industries, BASF announced its plan to expand its polymer dispersions production capacity by adding a second production line at its Huizhou site in the Daya Bay Petrochemical Industrial Park in Guangdong province. The new line will support advanced innovations with acrylics and styrene butadienecontaining dispersions, enabling agility and sustainable growth for customers in the South China market, which scheduled to start operations in 2024. BASF expanded its footprint in the personal care segment. A new Uvinul® A Plus production plant came on full stream in Jinshan Shanghai in September 2023. The state-of-the-art facility produces high-quality UVA filters included in the sunscreen formulations, further broadening the production footprint of its modern UV filter portfolio.
Related News
Growing capabilities in local production and R&D
- Expanded capacity for automotive refinish coatings in Jiangmen
- Enhanced Chemetall’s local production and innovation capabilities
- Rollout of multiple sustainability certifications at various plants in China
- Several sites celebrated milestones and anniversaries
At BASF, our strategy is to invest where our customers are located and where there is corresponding market growth. We continue to strengthen our advanced production footprint and R&D capabilities in China to support the growing demands of our local customers.
In Shanghai, BASF opened a new production plant for fuel performance additives at its Pudong site in August 2022, addressing the increasing regional demand for fuel performance additives and bringing greater supply stability and flexibility to customers in Asia.
In Jiangmen, BASF expanded the annual production capacity of automotive refinish coatings to 30,000 metric tons at BASF Coatings (Guangdong) Co., Ltd., strengthening BASF’s position as a leading and innovative coatings supplier to the automotive industry in China and the rest of Asia.
In 2022, BASF further enhanced its local production and innovation capabilities in China for its Surface Treatment business unit operating under the Chemetall brand. In October, BASF opened its first regional innovation center for applied surface treatment technology solutions, the Chemetall Innovation and Technology Center in Shanghai. In November, BASF inaugurated the company’s largest surface treatment production site in Pinghu, Zhejiang province. This will support local demand on high-performance surface treatment solutions of various market segments such as automotive OEMs and components, coils, general industry, cold forming, aerospace, aluminium finishing, and glass processing.
BASF has received multiple sustainability certifications to better support our customers to achieve their sustainability targets. BASF’s Thermoplastic Polyurethane (TPU) plant at the Pudong site is certified with the Global Recycled Standard (GRS) and Recycled Claim Standard (RCS), which validate the quantity of the recycled content used in the manufacture of TPU. BASF’s Polyol and Polyurethane Systems (PU) plant in Nansha, Guangzhou, is ISCC+ certified.
BASF has also received a biomass certification for its resins plant at Caojing site, as well as its paint manufacturing sites in Minhang and Caojing, operated by BASF Shanghai Coatings Co., Ltd. With this certification, BASF has launched its first automotive coatings using renewable feedstock, the ColorBrite® Airspace Blue ReSource basecoat, to its customers in China. Certified by REDcert² according to the biomass balance approach, this basecoat product enables around 20% reduction in product carbon footprint, as reviewed by the external sustainability consultant.
2022 marked an important year for the establishment of several BASF sites in Greater China. BASF Shanghai Coatings Co., Ltd., a 60:40 joint venture of BASF and Shanghai Huayi Chemical Co., Ltd., celebrated its 25th anniversary in October. The company manufactures and sells various high quality automotive OEM coatings products to customers in China. The Kaohsiung site, a key production site of the Care Chemical division, celebrated its 30th anniversary in November.
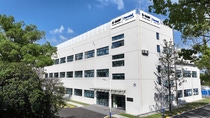
The Chemetall Innovation and Technology Center is BASF's first regional centre for applied surface treatment technology in Shanghai, China.
Partnering for low-carbon emission projects
-
“Sustainability Covalence” celebrated its 1st anniversary, promoting Product Carbon Footprint calculation methodology and low-carbon procurement
-
Collaborated with Sinopec, Baowu and Shell to explore CCUS Project
-
Collaborated with Huayuan Group on sustainable and innovative solutions
-
Partnered with China BlueChemical and Wuhuan Engineering to promote low-carbon development and utilization of marine gas resources
BASF celebrated the first anniversary of “Sustainability Covalence” with its founding partners in Hefei, Anhui province in October 2022. During the forum themed “Unlimited Vitality", which was co-organised by BASF and one of the co-founding partners – Huaheng Biotechnology – BASF shared its carbon calculation methodology and called for action on low-carbon procurement along the value chain.
BASF, Sinopec, Shell and Baowu signed a Memorandum of Understanding in Shanghai in November 2022 on an open-source Carbon Capture, utilization and storage (CCUS) project with a scale of tens of millions of tons per year in East China. The four partners aim to develop a supply chain of low-carbon products and to contribute to the development of the CCUS industry and China’s “dual carbon” targets.
BASF and Huayuan Group – a major Chinese player in the industry of high-end manufacturing, new energy, and advanced materials – formed a strategic partnership on sustainable and innovative solutions. Leveraging BASF’s deep know-how and extensive innovative solutions in the chemical industry, both companies will cooperate closely in metal pre-treatment technologies, pharmaceutical materials, and sustainable packaging materials.
BASF signed a joint development agreement with the leading natural gas producer China BlueChemical Limited Company, and the chemical engineering company Wuhuan Engineering Co., Ltd., to promote low-carbon development and utilization of marine gas resources. BASF’s solution helps to improve process energy efficiency and carbon efficiency beyond existing commercial catalyst and process technology.
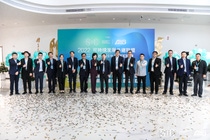
In October 2022, BASF celebrated the first anniversary of the "Sustainability Covalence" with its founding partners in Anhui province.
- Teamed up with REEF Technology to improve quality of plastic recyclate materials
- Launched innovative industrial eco-packaging with Nippon Paint China
- Formed partnership with local start-up Ingredi and invested in its equity
- Co-developed Paving Integrated Photovoltaic panels with Solar Earth
At BASF, sustainable solutions are often born through crossindustry co-creations. In 2022, BASF collaborated on innovative solutions for low-carbon development, plastic recycling, improved industrial packaging materials, and impactful sustainable progress across industries.
To develop state-of-the-art recyclate formulations for applications used in the automotive, packaging and consumer industries, BASF signed a strategic cooperation agreement with Zhejiang REEF Technology Co., Ltd. BASF will provide newly launched IrgaCycle™ additive solutions, technical consultancy and support on recycled polymer formulations conducted at BASF’s test facilities, co-creating with REEF Technology to support the plastic circular economy and to contribute to the increase of the percentage of mechanically recycled content.
BASF and Nippon Paint China, the leading coatings manufacturer, jointly launched an eco-friendly industrial packaging which has been adopted by the Nippon Paint dry-mixed mortar series products. With BASF’s water-based acrylic dispersion Joncryl® High-Performance Barrier (HPB) as the barrier material, the new packaging material is commercialized for the construction of dry mortar products of Nippon Paint. With excellent vapor and water resistance properties, Joncryl® HPB can replace plastics used in traditional packaging and significantly improve the recyclability of paper-based packaging, achieving the innovative application of “Paper Replacing Plastics” in industrial packaging.
BASF partnered with Ingredi, a local supplier of natural actives and solutions for the personal care industry. BASF also made a strategic equity investment into Ingredi. Established in 2017, Ingredi has shown strong capabilities in identifying new personal care active ingredients from natural plants found in the Himalayas. Through the equity investment from BASF, Ingredi will be able to extend its production facilities. In addition, BASF will jointly work with Ingredi on new solutions and commercialize them in the global personal care market.
BASF and Solar Earth Technologies Ltd. co-developed Paving Integrated Photovoltaic (PIPV) panels which can be installed on new or existing roads and other surfaces. The co-creation is part of the ongoing partnership between the two companies to develop innovative energy-efficient technologies that will advance the next wave of solar power applications.
To develop new talent in the automotive refinish industry, BASF supported the WorldSkills Shanghai 2022 Car Painting Category.
Collaborating towards sustainable mobility
- Ebusbar showcased a concept supercharging pile made with BASF’s innovative material solutions
- Collaborated on the promotion and extension of the value chain in automotive aftersales refinish industry with major OEMs
As the leading chemical partner for all major automotive OEMs, BASF continued to support China's new energy vehicle industry with advanced battery materials, automotive coatings, engineering plastics and polyurethanes in 2022. These innovative solutions contribute to the rapid development of e-mobility in China.
The charging infrastructure is key in enabling the widespread use of electric vehicles. The construction of charging piles has accelerated in tandem based on market needs and government investment. High-powered charging piles bring higher feasibility and better consumer experience in charging electric vehicles. BASF and Ebusbar showcased a concept supercharging pile made with BASF’s innovative material solutions. Ultramid® PA, Ultramid® Advanced PPA, Ultradur® PBT, and Elastollan® TPU are used in different components of the concept supercharging pile, including the housing of electronic parts, charging guns, breakers, switches, safety components, cables, and a cooling system.
BASF proactively collaborated with major automotive OEMs to promote and explore valued-added solutions along the value chain in the aftersales market. In 2022, BASF successfully launched a Customized Color Design project with LEXUS in China in an effort to improve LEXUS’s customer loyalty and increase its after-sales output. BASF also took this opportunity to show our refinish products directly to car owners. This project yielded a win-win solution for automotive OEMs, car dealers, and car owners.