Energetic innovators
For climate-conscious living with a small carbon footprint, access to alternative energy sources is crucial. Innovators and entrepreneurs from around the world are finding approaches to emissions reduction that meet the needs of individuals, households and companies.
Together, energy consumed in buildings and transport accounts for just over 30 percent of total greenhouse gas emissions. Private consumption, in domestic dwellings or for personal transport, makes up more than half of that. Climate-minded consumers already have choices if they want to stick within their personal carbon budget. They can buy renewable energy, or switch to an electric car, for example. Those solutions are not within everyone’s reach, however. Even in industry, where energy consumption accounts for around a third of global CO2 emissions, low-carbon technologies can be difficult to plug into existing plants and processes. To meet its emissions reduction targets, the world needs to make low carbon energy much more accessible.
A clean pair of wheels
Son Nguyen, founder and CEO of electric motorcycle company Dat Bike, is on a mission to make electric transport accessible to millions. Born and raised in Vietnam, Nguyen’s skills as a high-school computer programmer earned him a place at the University of Illinois, United States, and led to a role as a software engineer in a Silicon Valley firm.
Splitting his time between the United States and Vietnam made Nguyen acutely aware of the different directions the two countries were taking in mobility. Electric cars were becoming commonplace on the streets of California, but “at home in Vietnam, more people moving into cities led to lots of polluting gasoline-powered motorbikes on the streets.” Across Asia, he says, there are 250 million people who use “a gas guzzling motorbike” as their everyday transport. This made him think that electrifying those machines could be “a solution to a very impactful problem.”
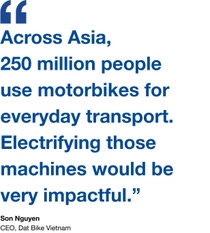
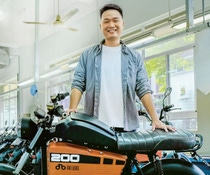
Dat Bike makes Vietnam’s first domestically produced electric motorbikes. The company aims to match gasoline machines for price and performance.
There was just one catch: Nguyen had no experience in motorcycle design, or electric powertrains, “so I quit my job and started learning.” Over the next few months, he put himself through a crash course in engineering to pick up critical skills, such as welding. Within a year, he had made his first prototypes. Showing them online attracted some early investors. It was time to go back home.
Arriving in Vietnam to set up Dat Bike, Nguyen had two priorities for his product: It should match its fossil-fuel counterparts for price and performance, and it should be locally manufactured to the highest degree possible. After a TV appearance, the tiny company was inundated with inquiries from potential suppliers and investors. Six months later, its first machines rolled off the production line. With more than 80 percent of its suppliers located in the country, Dat Bike’s Weaver model was Vietnam’s first domestically produced electric motorbike.
The machines are a hit. Dat Bike increased its manufacturing capacity fivefold during the first half of 2022, but its latest Weaver 200 model bikes were still sold out months in advance. So far, customers are willing to wait. “There’s nothing like it on the market,” says Nguyen. “Ride one for five years and the fuel cost savings alone mean you effectively get the bike for free.”
Now we're cooking with gas
In Ghana, 12,000 kilometers west of Vietnam, Enoch Kofi Boadu has built a business enabling customers to create clean energy for free. DAS Biogas builds and installs systems that can transform waste into cooking fuel. Biogas is a mixture of methane and carbon dioxide generated by bacteria that decompose organic material in the absence of oxygen. Today, it is produced on an industrial scale at plants fed by sewage or agricultural wastes. DAS Biogas, however, is creating household-scale units that are robust, cheap and easy to install.
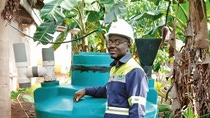
The DAS portable biogas plant transforms a household’s waste into enough fuel to meet at least half its cooking needs.
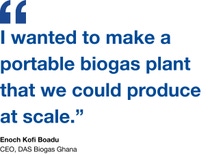
The idea was born when Boadu was a high-school science and technology teacher. “I used to run a lot of experiments with my students, and we started making biogas in small containers,” he recalls. “That made me realize that this technology had a lot of potential.” Boadu’s experiments have continued ever since. “We pursued different approaches, but I really wanted to make a portable plant that we could produce at scale and install across Ghana and beyond,” he says.
The first DAS Biogas Prefab1 plants entered the Ghanaian market during the summer of 2022. For 1,300 U.S. dollars, customers receive a biogas digester, a gas storage bag, and a single burner stove. “The whole system is made locally,” he explains. “The tanks are molded in plastic by a local company, and we also use local sources to weld the bags that store the gas.”
The plants can be installed outside a house to convert kitchen waste such as food, fruit and vegetable waste to cooking fuel. Or they can be built into it during construction to additionally convert sewage. The effluent undergoes further treatment in a secondary unit to ensure that the treated water meets all relevant environmental discharge standards, allowing it to be reused for garden irrigation or flushing toilets.
The system generates around one cubic meter of gas per day, enough to meet more than half the cooking needs of a typical Ghanaian household. This ultimately reduces the need to use LPG, electricity or wood. Each unit, says Boadu, saves between 3.7 and 5 metric tons of CO2 per year. By late autumn 2022, the company had made and installed 20 systems, and it plans to increase production fivefold in 2023.
Full steam ahead
While DAS Biogas and Dat Bike are scaling down low-carbon technologies to meet the needs of homes and individuals, BASF is now scaling up approaches that work in households to an industry level. About half of BASF’s current carbon footprint comes from energy generation on its sites, and of that 11 million tons, 6 millions comes from the production of steam. “Finding ways to reduce emissions associated with steam has become a significant focus over the past two years,” says Bart Van Assche, Vice President Global Infrastructure Technology at BASF, based in Ludwigshafen, Germany.
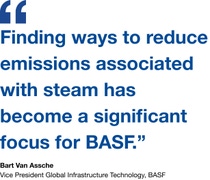
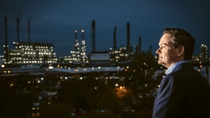
Each of BASF’s five largest production sites generates enough waste heat to meet its own demand for steam.
One promising approach is the transformation of waste heat into useful energy using a technology that is already found in many homes: the heat pump. Heat pumps use the compression and expansion of a gas to transfer energy from a lower temperature source to a higher destination. Since every kilowatt hour of electricity used to run the pump produces several kilowatt hours of heat, they are an efficient way to keep homes warm. “In each of our five largest production sites, we know that there’s more than enough energy in waste heat to meet our steam requirements,” says Van Assche.
The heat pumps Van Assche’s team is investigating differ from domestic units in two important ways: temperature and scale. “Temperatures will be much hotter and will generate steam at more than 120 degrees Celsius.”
That low-pressure steam can then be compressed, heating it even more, and injected into the steam grid at a site. Running the heat pumps and compressors using electricity from renewable sources will contribute significantly to reducing CO2 emissions. Industrial heat pumps will also be orders of magnitude bigger than home units. “We are currently doing detailed studies for the first heat pump projects, and they are the size of football fields,” he says.
The new heat pumps will be part of a multi-pronged approach to steam decarbonization. BASF is also looking for ways to reduce steam demand, such as by replacing steam-powered drives with electric motors, and it is investing in boilers powered by renewable electricity.
There won’t be a one-size-fits-all answer to the low-carbon energy challenge. But ongoing innovation in a wide range of technologies means people have an ever-increasing chance of finding sustainable solutions to suit their needs.
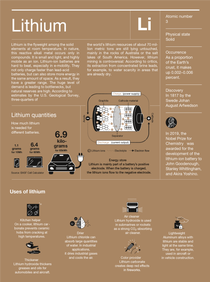