Ποιοι είμαστε
ecovio® – Biobased and compostable polymer
BASF’s bioplastic is a high-quality, completely compostable polymer. It consists of the biodegradable BASF polymer ecoflex® and polylactic acid (PLA), which is derived from renewable resources based on sugar.
First production application of the compostable plastic ecovio in coffee capsules
Products made out of ecovio® are just as high-performing and strong in use as conventional plastics. The polymer ecovio has already been able to prove itself in applications such as organic waste bags and agricultural films. Furthermore, the first application for the injection molding grade ecovio IS is now used for certified compostable coffee capsules and an aroma-tight outer packaging.
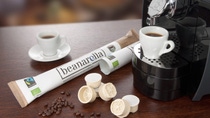
The research behind
Cross-section through the ecovio barrier: The scanning electron micrograph shows the extremely thin coating on cardboard packaging.
Who are the researchers behind the innovation ecovio? We spoke to two ecovio experts and took the opportunity to look behind the scenes. Dr. Robert Loos has accompanied the development from the outset, and Dr. Maximilian Lehenmeier has been involved since 2012 in broadening the applications for ecovio.
Dr. Loos, what's so special about ecovio?
Loos: The special thing about this material is that it's a mixture of biodegradable ecoflex from BASF and polylactic acid manufactured from renewable resources to produce a fully compostable plastic, which also consists partially of renewable raw materials. What's impressive is that products made from ecovio now have the same properties as conventional non-biodegradable standard plastics and can be processed just as easily.
Dr. Lehenmeier, what everyday applications are improved by using ecovio?
Lehenmeier: One good example is coffee capsules. Coffee capsules produce a very large amount of residual waste, although coffee powder is actually a valuable fertilizer and compostable. When we use ecovio for the capsule material, the capsules can be disposed of as bio-waste. It is important, however, for the material to fulfil the high barrier requirements for coffee packs, such as moisture, oxygen and aroma. At present this can only be achieved with special compostable capsule packaging: however, research is already in progress into suitable solutions for the coffee capsule of the future. The capsule also has to withstand coffee brewing in high-pressure coffee machines, while still remaining fully compostable. We have achieved this and, through our research, have therefore contributed to reducing unnecessary waste.
What other developments are planned for ecovio?
Loos: So far the product has mainly been used as mulch film, shopping bags and biowaste bags. We have also been researching for some time into further applications for ecovio. We can adapt the material properties, such as stiffness or transparency, to match the application by varying the quantitative composition of the components. Other processing methods such as injection molding or deep drawing are therefore possible and open up new applications such as the coffee capsules already mentioned. Another direction in which we are currently researching intensively involves compostable hot drink lids for paper cups, for which the cups are also coated with ecovio instead of polyethylene. This means we are concentrating particularly on developing whole systems.