Chi siamo
In fase di sviluppo le batterie che alimenteranno il futuro

Presso il Battery Materials Lab. di Amagasaki in Giappone, i ricercatori BASF stanno sviluppando materiali innovativi destinati a migliorare le prestazioni delle batterie agli ioni di litio e ad aumentare l’autonomia di guida dei veicoli elettrici.
Lunedì mattina ore 9, il Dr. Masaki Sekine, un chimico organico, siede al suo computer e legge le e-mail ricevute dai colleghi con cui collabora in Germania e in altre località nella rete internazionale BASF di impianti R&S di materiali per batterie. Sekine lavora presso il Battery Materials Lab di Amagasaki, Giappone, ultimo arrivato in questa rete, inaugurato all’inizio del 2014. Sta aspettando il feedback dei colleghi sui suoi tentativi di creare “una molecola totalmente nuova, mai esistita in precedenza.”
Sekine fa parte del team che sintetizza sostanze innovative da utilizzare come additivi negli elettroliti, il mezzo chimico che consente il flusso di ioni di litio tra un elettrodo positivo di una batteria, il catodo, e il suo elettrodo negativo, l’anodo. I nuovi additivi influiscono sulle reazioni elettrochimiche all’interno della batteria e possono quindi determinare le prestazioni della batteria.
I tipi di additivi creati da Sekine dipendono dagli aspetti che i clienti vogliono migliorare nelle loro batterie. Molti dei clienti del laboratorio sono produttori giapponesi di batterie agli ioni di litio che stanno sviluppando nuove batterie per i veicoli elettrici. Stanno cercando di ottenere miglioramenti quali una maggiore densità energetica, una maggiore stabilità alle alte temperature o un aumento nelle prestazioni in termini di vita ciclica, cioè il numero di volte in cui la batteria si può scaricare e caricare.
Per creare un nuovo additivo utilizza un processo di sintesi organica. La sintesi dell’additivo avviene in un solvente. Una volta avvenuta la reazione, questo solvente deve essere separato.
“La purificazione dell’additivo è la parte impegnativa del processo,” dichiara Sekine. “In molti casi le cose non vanno come previsto. E nella maggior parte dei casi un singolo ciclo di purificazione non offre una purezza sufficiente per soddisfare le severe specifiche per un additivo per batteria. Anche le più piccole impurità possono provocare reazioni incontrollate e potrebbero compromettere in misura significativa le prestazioni della batteria, come aumentare il rischio che la batteria si scarichi quando non viene utilizzata.”
Lavorare in una rete globale è stimolante e aiuta i team a trovare rapidamente le soluzioni. “Una volta ero bloccato con una sintesi,” ricorda Sekine. “Teoricamente erano disponibili vari percorsi sintetici, ma non riuscivo a farli funzionare. Sono stato quindi contattato da un collega tedesco che mi ha suggerito un percorso catalitico alternativo molto più efficace.” Questo feedback e la collaborazione aperta sono fondamentali. Questo è il motivo per cui il prossimo passo per Sekine consiste nel discutere i suoi risultati con il gruppo prove elettrochimiche del laboratorio.
Prove 1, 2, 3, 4 ...
Un membro del gruppo di prova è la Dr.ssa Zhen-Ji Han che proviene da Yanji in Cina ed è entrata a far parte del team nel 2013. Collabora allo sviluppo di formulazioni elettrolitiche e conduce prove elettrochimiche per le batterie che usano materiali anodici di nuova generazione. Il suo lavoro consiste nel testare gli ultimissimi additivi sintetizzati.
Han porta il nuovo additivo alla camera di Assemblaggio Celle dove, indossando tuta da lavoro, guanti di protezione e occhiali di sicurezza, lo miscela in un elettrolita di base preparato e quindi inietta la soluzione in una cella di prova. Questo le permette di esaminare le proprietà elettrochimiche della cella. Le prestazioni della batteria si deteriorano con l’uso ma anche con il tempo. È quindi necessario testare ognuno di questi aspetti: prestazioni, vita di calendario e vita ciclica. Per testare quest’ultimo aspetto, la cella viene collocata in un ciclatore dove, per alcune settimane o mesi, viene ripetutamente caricata e scaricata. Han discute le sue scoperte con il gruppo di sintesi. “Poiché ne sappiamo di più sulle interazioni chimiche della batteria, possiamo consigliare ai sintetizzatori quali parti degli additivi funzionano bene o meno bene e come riprogettare al meglio le loro strutture molecolari,” afferma.
“ La nostra esperienza nello sviluppo dei materiali catodici ed elettrolitici e la nostra capacità di collaborare come una squadra ci differenziano dagli altri.”
Dr. Martin Schulz-Dobrick, Direttore del Battery Materials Lab, Amagasaki, Giappone
Soddisfare esigenze diverse
Molto del lavoro eseguito presso il laboratorio è fatto su misura per le esigenze individuali dei clienti. È qui che entra in gioco Hiromu Sugiyama. Il ricercatore senior nello sviluppo dei catodi lavora direttamente con i clienti aiutandoli a realizzare i loro obiettivi prestazionali. Questo include il controllo dei dati delle prove sui materiali catodici per accertarsi che il contenuto di metallo di transizione sia adatto agli obiettivi prestazionali o verificare se le dimensioni e la forma delle particelle del materiale miglioreranno o ostacoleranno il conseguimento di un obiettivo prestazionale.
“Dobbiamo sempre considerare in che modo il catodo si interfaccia con gli altri componenti nella batteria,” spiega Sugiyama, che è entrato a far parte del team nel 2014. “Le prove e le analisi vengono quindi effettuate in stretta collaborazione con altri team di ricerca.”
Tutti sotto lo stesso tetto
“ Il laboratorio di Amagasaki è speciale per vari motivi,” dichiara il Dr. Martin Schulz-Dobrick, capo della struttura. “È il primo impianto di BASF della regione Asia/Pacifico a combinare lo sviluppo di materiali catodici, materiali elettrodici ed elettrolitici con le tecnologie applicative. Non solo conduciamo ricerca di base su questi materiali partendo da zero, ma supportiamo anche i nostri clienti nella prototipizzazione delle batterie.” Un esempio del lavoro applicativo basato sulle esigenze specifiche di un cliente è lo sviluppo congiunto di una ricetta per un elettrolito. “Stiamo progettando e costruendo congiuntamente batterie di prova che ci permettono di testare i nostri materiali in condizioni vicine alle esigenze dei clienti e quindi accelerare l’intero sviluppo,” spiega il capo del laboratorio.
E, in maniera significativa, l’impianto riunisce le diverse aree di ricerca sotto lo stesso tetto. “Questo è il grande vantaggio del nostro laboratorio,” dice Schulz-Dobrick, che si è trasferito in Giappone nel 2013 dalla sede BASF in Germania. “La nostra esperienza nello sviluppo di materiali catodici ed elettrolitici e la nostra capacità di collaborare come una squadra ci differenzia da altri fornitori di materiali che generalmente possono fornire ai produttori di batterie materiali elettrolitici o catodici. Noi siamo specializzati in entrambi.”
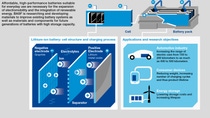