Produkti
Infinergy® ‒ Small Beads, Big Possibilities
Infinergy® is the world’s first expanded thermoplastic polyurethane (E-TPU). The closed-cell, elastic particle foam combines the properties of TPU with the advantages of foams, making it as elastic as rubber but lighter.
The elastic particle foam Infinergy® can be used anywhere, where a combination of low weight, excellent mechanical properties, and long-term durability is needed. Infinergy® panels can be processed on standard slitting lines, die cutting and water-jet cutting machines.
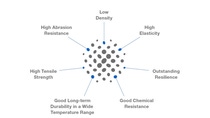
Properties
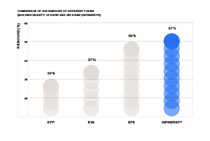
Like its starting material TPU, Infinergy® is noted for having high elongation at break, tensile strength and abrasion resistance as well as good chemical resistance. In addition, the innovative particle foam remains highly elastic and soft over a wide temperature range.
The feature of Infinergy® that is particularly striking is its high resilience. Tests of the resilience elasticity under ISO 8307 (the ball rebound test) and under DIN 53512 (using a defined pendulum hammer) show that Infinergy® achieves a rebound of over 55%. This is therefore significantly higher than comparable particle foams such as expanded polypropylene (EPP) at 30%, ethylene vinyl acetate (EVA) at 37% or expanded polyethylene (EPE) at 50%. Infinergy® does not lose its excellent resilience even under a continuous load.
Dynamic mechanical analysis has shown that, even at extremely low temperatures of -20°C (-4°F), Infinergy® still has a low dynamic modulus, is very soft and stretchy and thus does not go stiff.
Elastic Even Under Continuous Load and over Wide Temperature Range
High-frequency fatigue test:
- Dynamic loads of 250 kPa and 5 cycles/second
- Thickness of the test piece after 40,000 cycles:
EPE: 22 percent (9 mm), Infinergy®: 93 percent (37 mm) - Density: 30 kg/m³ (EPE), 265 kg/m³ (Infinergy®)
--> Dynamic mechanical analysis: Infinergy® stays elastic up to minus 20°C.
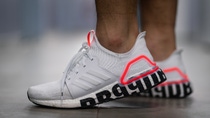
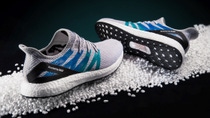
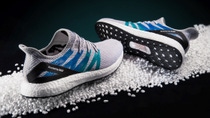
Applications
Processing
In principle, Infinergy® can be processed on the same molding machines which are designed for processing of expanded polypropylene (EPP). A steam chamber pressure of at least 5 bar is necessary. During processing, the steam pressures are usually in the range of 1.6 to 2.2 bar, depending on the geometry and density of the molding. Both crack splitting and pressure filling are possible methods that can be applied here. Appropriate injection systems should be used.
In addition, because polyurethane binders adhere so well to Infinergy®, there are other processing techniques such as gluing and foam sealing of the beads. This procedure enables large-scale processing of Infinergy®.
Converters can process panels made from Infinergy® on conventional splitting machines, punches and water jet cutting machines.
Environment and Recycling
Infinergy® is compliant with the RoHS directive and does not have to be labeled under dangerous goods regulations.
Information on other regulations, e. g. GADSL, will be provided on request.
Infinergy is also recyclable.
Contact us
Get in touch. We would love to help you start redefining what's possible.
Featured News
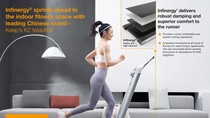
Infinergy sprints ahead in the indoor fitness space with Keep’s latest treadmill
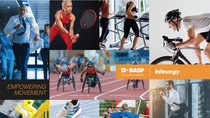
BASF launches “Empowering Movement” brand strategy for Infinergy
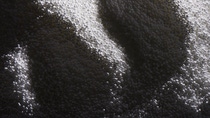
New size, new color, new processing method – Infinergy® picks up the pace
BASF receives top 10 “Sports Surfaces Materials Supplier” award in China
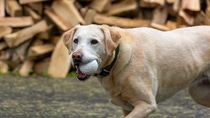
Plymouth Foam to launch a new generation of pet toys at SuperZoo 2019 based on BASF Infinergy material
Tailor-made Solutions
Tailor-made for individual needs: We support our customers in developing application-oriented solutions.