Media
Sustainable construction in face of climate change
BASF offers durable solutions for the housing construction market to help withstand future disasters.
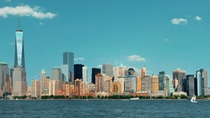
In the past few decades—rising temperatures have worsened extreme weather occurrences; chunks of ice in the Antarctic have broken apart; and wildfire seasons are months longer. As for the future, continued ocean and atmospheric warming will likely cause sea levels to rise for many centuries at rates higher than that of the current century, while almost half of the U.S. population lives in relatively high-population-density coastal areas, according to the National Oceanic & Atmospheric Administration.
Nine billion people will live on this planet by 2050. Three quarters of the population will live in cities. The topic of climate change is clearly not going away.
“We’re not even dealing well with disasters that we have today. Two thirds of the communities that are impacted by hazardous events do not have updated building codes,” said Ryan Colker, Vice President, Innovation & Executive Director, Alliance for National & Community Resilience and the International Code Council, during the roundtable dinner at the fourth annual Atlantic Summit on Infrastructure + Transportation Summit in Washington, D.C., underwritten by BASF. “We’re not getting to the baseline level of dealing with disasters and hazards that we have today, let alone what’s coming out into the future.”
The growing urbanization of the population will require new concepts for housing and construction. That’s where BASF comes in—closing the flooding risk/disaster gap by offering resilient construction solutions. With the company’s chemistry, buildings can be more durable and require fewer resources for maintenance. Chemistry also makes buildings more efficient, thus protecting the environment. The German corporation created Disaster Durable Solutions in May 2012, which represents the company’s long-term commitment to address the high costs of disasters. It improves the disaster resiliency of homes and businesses through stronger building envelopes.
Living proof of resilient design is best exemplified by BASF with a project in Breezy Point, Queens, NY, which was mentioned during the panel discussion titled Sustainable Construction: Resilient Infrastructure, presented by BASF during the summit. The chemical company was one of several organizations, including FEMA, to partner on rebuilding a 1955 home destroyed by Hurricane Sandy’s post winds and storm surge. Today—a new residence built from spray polyurethane foam, graphite-infused polystyrene and concrete stands in its place. Using best practices in coastal construction and an energy-efficient design, the house is a model for the future.
“Breezy Point is a showcase of a project that can work that’s both sustainable and resilient,” said Deane Evans, Executive Director, NJIT Center for Building Knowledge & NJIT Center for Resilient Design who partook in the BASF panel discussion on resilient construction.
“Breezy Point is a location that was heavily impacted by Superstorm Sandy. BASF and partners came together and saw this as an opportunity to build a model for resilient home construction using existing sustainable construction technology,” added Grace Showalter, VP, BASF Performance Materials Construction, North America, BASF, who also participated in the panel.
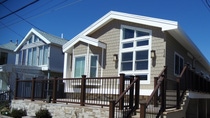
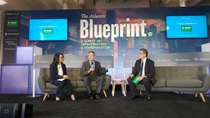
During the project’s rebuild, BASF used its disaster-resilient products that made the home stronger, more durable and more comfortable for the occupant. One of the products used was—SPRAYTITE—the closed-cell spray polyurethane foam—which insulates roofs, walls and all types of structures in the residential market. Products such as this one meet voluntary and risk-specific standards that provide crucial property protection and comply with Insurance Institute for Business and Home Safety’s FORTIFIED Home programs. Recommended by FEMA for homes disaster-prone areas, BASF’s spray polyurethane foam (SPF) mitigates the effects of water and, when properly used in a roofing system, can sustain extreme impact from hail damage compared to a traditional roofing system. Additionally, the foam offers greater wind uplift resistance than many alternatives when fully adhered to the building structure.
The German company is no stranger to other resilient products that stand the test of time. For erosion control and protection, Elastotite ROCK GLUE is an open-pore revetment solution that maintains structural integrity and can be used in a variety of applications, including shorelines, rivers, drainage channels and other embarkments. It also offers design flexibility for integration into natural landscapes. The monolithic, porous structure easily confirms into various shapes and promotes natural re-vegetation.
“For every dollar spent for pre-disaster mitigation, we save $11 in recovery. Also, in the last five years, the U.S. has spent $50 billion on disaster recovery, that’s $10 billion each year,” said Showalter, of BASF. “That kind of spending is not sustainable, and therefore, to me, key and meaningful progress has to happen with pre-disaster mitigation with how to rebuild for sustainability and for resilience.”
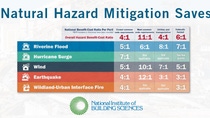
As for the future of resilient control in face of growing climate change, collaboration is key across various organizations, according to Showalter.
“We have to work with partners because the industry cannot do it alone,” she added. “We have to work with designers, with architects, with local government, with codes officials, to come together and design and build, and then go from a locale up; it’s about education and prevention.”
As climate change will continue to accelerate disasters, aside from turning to more durable construction materials, solutions such as smart design and retrofitting; innovation in technology and materials in design; the need for education and growing public awareness will be key drivers leading to policy change, according to experts.
“New construction has the opportunity to do a double whammy in the sense that if you design and build well—you can actually reduce the impacts of climate through energy efficiency,” Evans concluded. “If you can combine that with resilient construction at the same time—then you win and prevent impacts of these hazards.”
Published on February 24, 2020 by Anna Spiewak.
For media inquiries or to repurpose this article, please contact Lisa Brown.