Digitalisierung
Manufacturing
Durch den Einsatz von digitalen Technologien und die Nutzung von Daten erhöhen wir die Effektivität unserer Anlagen und die Effizienz unserer Produktionsprozesse. Mit mobilen Endgeräten haben wir Zugang zu relevanten Informationen für unsere tägliche Arbeit. Die Verknüpfung von Produktions- und Geschäftsprozessen ermöglicht uns, schneller und besser Entscheidungen zu treffen.
Augmented Reality
Die digitale Anwendung „Augmented Reality“ unterstützt unsere Mitarbeiter bei ihren täglichen Aufgaben in den Anlagen durch direkten und schnellen Zugang zu benötigten Informationen mit mobilen Endgeräten, wie Tablets oder Smartphones, die speziell für das Arbeiten in den Anlagen konstruiert und ausgestattet sind. Somit können wir die Effizienz unserer Abläufe erhöhen und den Wissenstransfer nachhaltiger gestalten.
Predictive Maintenance
Bei der Anwendung „Predictive Maintenance“ geht es um die Vorhersage des Funktionszustands von kritischen Anlagenteilen und Komponenten wie zum Beispiel Verdichter oder Wärmetauschern. Mit Hilfe von Sensoren werden Live-Daten über Betriebszustände ermittelt und mit einer speziellen Analyse-Software – unter Einbeziehung historischer Prozessdaten – modelliert und ausgewertet. Unser Ziel: die Vorhersage des optimalen Zeitpunkts für Instandhaltungsmaßnahmen. So können wir ungeplante Reparaturen und Ausfälle reduzieren und die Abstimmung von Instandhaltungs- und Produktionsprozessen optimieren.
Beispiele für kritische Assets und Prozesseinheiten
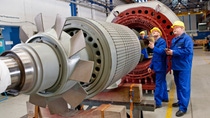
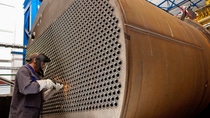
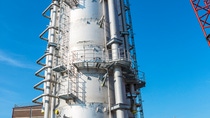
Strom- und Dampferzeugung im Kraftwerk 4.0
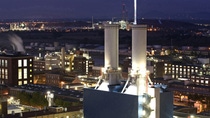
Unser Ludwigshafener Verbund benötigt pro Jahr rund 20 Millionen Tonnen Dampf. Dieser wird in den Produktionsbetrieben und den drei werkseigenen Kraftwerken erzeugt. Zudem stellen die Kraftwerke den Großteil des Stroms für den Standort her. Teilweise sogar mehr als benötigt, so dass Strom ins öffentliche Netz eingespeist werden kann.
Der Handel mit Strom ist allerdings ein komplexes Geschäft, da die Marktpreise im Viertelstundentakt schwanken. Computerprogramme helfen, zum bestmöglichen Zeitpunkt zu kaufen oder zu verkaufen. Dazu bedarf es jedoch einer möglichst genauen Vorhersage, wie viel Dampf und Abhitze die Betriebe am Standort liefern, wie viel Dampf die Kraftwerke beisteuern müssen und wie viel Strom benötigt wird. Auch dies schwankt, abhängig von Jahreszeit, Wetterlage und wirtschaftlichen Rahmenbedingungen.
Bisher lief die Ermittlung des Gesamtbedarfs über händisch zusammengeführte Einzelprognosen der Betriebe. Ein neues, auf großen Datenmengen basiertes, statistisches Modell liefert jetzt noch genauere Berechnungen: Die Software beachtet unter anderem historische und aktuelle Informationen zu Produktionsabstellungen, Wetterdaten sowie Konjunkturindizes. Das Programm sucht nach Zusammenhängen und stellt Verbindungen zum Energiebedarf her.
Mit Erfolg: Die Prognose für den Dampfbedarf konnte bereits um bis zu 60 Prozent verbessert werden. Die alte Vorgehensweise wird nun schrittweise abgelöst und auf andere Bereiche angewendet. Mit dieser Big Data basierten Software profitiert BASF zusätzlich beim Stromhandel, da die Preisentwicklung besser vorhersehbar ist.