Factbook
Innovation
Innovations based on chemistry play a pivotal role in overcoming the greatest challenges of our time. Our activities are aimed at developing new products, entering new markets, further increasing our productivity and reducing the carbon footprint of our existing products. We are intensively working together with our customers on innovative products and processes for a sustainable future.
Innovation has always been the key to BASF’s success. The knowledge and skills of our highly qualified employees are our most valuable resource and the source of our innovative strength. In 2024, approximately 10,000 employees worldwide were working in research and development (R&D).
In 2024, we generated sales of around €11 billion with products launched on the market in the past five years that stemmed from research and development activities. In the long term, we aim to further increase sales and earnings with new and improved products – especially with products that make a positive sustainability contribution in the value chain.
Our R&D expenses amounted to €2,061 million in 2024 (2023: €2,130 million). R&D activities in our operating divisions, which are mainly application and customer-related, accounted for 87% of this figure. Cross-divisional and strategic topics were responsible for 13% of these expenses.
Our innovation focus is on developing new and improved products and solutions that offer our customers competitive and sustainability advantages. By helping them to reduce their carbon footprint, use resources more efficiently, or manufacture products in a more environmentally friendly way and recycle them, we ensure our long-term competitiveness and, at the same time, play a role in decoupling growth from the consumption of limited resources.
Research and development expenses by segment 20241
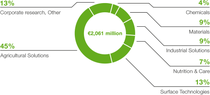
In the area of electromobility, for example, we develop materials for batteries and electric powertrains in close cooperation with vehicle manufacturers to enable safe and efficient driving. We are working on innovative depolymerization processes that can be used in the recycling of foam mattresses or the rigid foam found in fridges as well as on circular solutions for textiles. We also develop biodegradable polymers for household and personal care applications as well as biodegradable UV absorbers for sunscreen, and thus help our customers achieve their sustainability targets.
Our R&D units explicitly address the industry-specific needs of our customers. Customer-focused activities are directly integrated into the operating divisions. Research activities that are relevant to several operating divisions are bundled in the cross-functional global division Group Research. It supports the R&D activities of our operating divisions and drives forward cross-divisional projects on topics relevant to the entire Group, such as avoiding CO2 emissions in chemical processes and products, energy efficiency and recycling technologies. The unit is globally positioned with research centers in Asia Pacific, Europe and North America. Together with the research and development units in our operating divisions, Group Research forms the core of our global research network.
We use corporate funding to finance research activities that are of broad relevance to the BASF Group and go beyond the industry-specific focus of the individual operating divisions, such as digital tools, new analytic methods, catalytical processes and biotechnological methods.
The number and quality of our patents also attest to our power of innovation and long-term competitiveness. In 2024, we filed 1,159 new patents worldwide, of which 44.5% were for innovations with a particular focus on sustainability. The Patent Asset Index, a method that compares patent portfolios, once again ranked BASF among the leading companies in the chemical industry in 2024.
Global presence
The largest site in our research network is Ludwigshafen in Germany. A new Catalyst Development and Solids Processing Center was opened there in December 2024 to bring process innovations and new chemical catalysts to market faster. Innovation Campus Shanghai in China is our largest research and development site in Asia Pacific. Here, we work on new products and processes for a variety of customer industries, including in growing sectors such as electromobility and renewable energies.
Our global network of top universities, research institutes and companies forms a further part of our Know-How Verbund. It gives BASF direct access to external scientific expertise, talented minds from various disciplines as well as new technologies. Our eight academic research alliances bundle partnerships with several research groups in a region or with a specific research focus.
For more information on our academic research alliances, see BASF Report 2024