Magazine
Energy transition at BASF
BASF is serious about climate protection and intends to make increasing use of emission-free wind and solar energy at its sites. Fluctuating production volumes and high electricity procurement costs are just some of the challenges that still have to be overcome.
The BASF site at Schwarzheide in the German state of Brandenburg, located in the Lower Lusatia lignite-mining region, has what it takes to become a laboratory for the energy transition in the chemical industry. One wind turbine after another extends its blades into the sky north of the BASF site, not far from this landscape dominated by open-cast coal mining. More than 360 megawatts of capacity from renewable energy sources have now been installed in and around Schwarzheide, and another 300 megawatts are planned. This means much more renewable energy is being produced than consumers in the region are using – and in some cases it is actually more than the grid can take. “Our situation is a glimpse into the future,” says Dr. Robert Preusche, Head of Renewable Energy Transformation for BASF at Schwarzheide. “The proportion of renewables in the electricity mix around Schwarzheide is already at levels that the German federal government is seeking nationwide by 2030 or 2040.” However, a few technical and political challenges still have to be overcome before BASF can use energy from renewable sources on a large scale at Schwarzheide or other sites.
Verbund sites need a lot of energy
Even if there is a lull in the wind or thick cloud cover, the quantities of electricity from renewable sources that are needed for production will still have to be available in the future. BASF’s six major Verbund sites worldwide, in particular, need a lot of energy. These include Ludwigshafen, Germany, where more than 200 production facilities, energy supply, logistics, and infrastructure are intelligently integrated and connected with each other. In this Verbund system, one plant can, for example, use another plant’s waste heat as energy and use by-products as raw materials for making other products. Energy at Verbund sites is currently produced as far as possible in BASF’s own highly efficient gas and steam power plants, which emit around 50 percent less CO2 per megawatt-hour of energy produced than the electricity mix in the public grid.
“We can restructure our internal energy supply to enable us to use electricity from renewable sources instead of natural gas, but the volumes of electricity that the site will then need are not yet available in the region and cannot yet be transported to Ludwigshafen through the existing power networks,” says Markus Scheuren, Head of Energy Verbund Management & Legislation at BASF in Ludwigshafen.
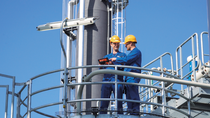
Grid charges and levies increase the procurement cost of green electricity
High grid charges and levies for electricity procurement are another major obstacle to using more green electricity in production in Germany. “As soon as we buy in electricity, whether it is green or grey, from outside, we have to pay levies on top of the regular electricity price,” explains Dr. Roland Merger, who is responsible for renewable energy for BASF worldwide. “If we produce the electricity locally in the existing facilities at our own sites, those network charges and levies do not apply. We can only produce competitively by using our own electricity.” He adds that usually there is simply not enough space to produce large quantities of green electricity ourselves at BASF sites.
We are approaching the energy transition with determination and are building a climate-friendly chemical industry.”
For this reason, Jürgen Fuchs, Chairman of the Management Board at BASF Schwarzheide, stresses that “we need renewable electricity at competitive prices in order to be successful. Only then can we implement our plans in Brandenburg and really make use of renewable energies – in particular, for the new facility for making battery materials from 2022.”
Despite all the challenges that still have to be met, a total of 23 locations in Europe, North America and Asia were already being supplied with emission-free electricity in 2019 – either through the direct purchase of renewable electricity or through renewable electricity certificates. For example, in Canada, BASF and Bullfrog Power, a large Canadian renewable energy provider, entered into a partnership in 2018. Since then, BASF has been using renewable electricity for its Canadian headquarters and other production facilities based in the country’s most carbon-intensive provinces, thereby decreasing its national carbon footprint by 50 percent in Canada. By the early summer of 2020, BASF had reduced its CO2 emissions by about 6,000 tons.

BASF developing low-emission production processes
Every one of these steps is closely connected with BASF’s sustainability strategy, which has climate protection as a central component. “The path leading to the energy transition is a huge challenge for the energy-intensive chemical sector in particular. This makes it especially important for us to approach this challenge with creativity and determination and build a climate-friendly chemical industry,” says Dr. Martin Brudermüller, Chairman of the Board of Executive Directors at BASF. In recent decades, BASF has already significantly reduced its CO2 emissions by optimizing its energy generation and its production processes. To reduce greenhouse gas emissions even further, BASF researchers are currently working to develop fundamentally new, low carbon production processes, which are due to come into use from about 2030, as a matter of high priority. “We are concentrating here on the production of basic chemicals, since these are responsible for about 70 percent of the chemical industry’s greenhouse gas emissions,” Brudermüller says. “With electrification and new processes involving power from renewable sources, we may be able to produce those basic chemicals with almost zero emissions in the future. This will roughly triple our electricity demand at Ludwigshafen alone.”
Schwarzheide investing in the energy transition
At the Schwarzheide energy-transition laboratory, meanwhile, BASF’s in-house gas and steam-turbine power plant is already being modernized. BASF is investing €73 million to enable it not only to generate electricity and steam with an even smaller carbon footprint in the future, but also to use wind and solar power to supply its production facilities. “We aim to use our pilot project to prove that renewable energies can be used on an industrial scale despite the chemical industry’s great need for security of supply,” Management Board Chairman Fuchs explains. The modernized power plant at the BASF site will be better able to absorb fluctuations and to be powered up or down within minutes, depending on whether or not enough electricity from renewables is available.
In addition, a plan is currently being worked out to test two different battery storage systems. The first involves stationary NAS® batteries, which are based on tried-and-tested sodium-sulfur technology from Japanese manufacturer NGK Insulators Ltd., and are being distributed and refined by BASF subsidiary BASF New Business. For the second, BASF’s Intermediates division is supplying one of the two electrolytes for organic redox flow batteries from the energy storage company JenaBatteries. It is intended that the tests of battery storage systems will use renewable energies to ensure a stable and reliable supply. “It is important that we at Schwarzheide act here and now to set a course and to try out integration, because the chemical industry in the future will be based much more firmly on electricity from renewable sources,” Fuchs stresses.