기후를 위한 변화
BASF’s Commitment to Climate Protection in Korea
In an effort to respond to climate change, BASF aims to achieve carbon neutrality by 2050. Against this backdrop, BASF in Korea is also contributing to achieving net zero goal with climate-friendly solutions providing low-product carbon footprint products.
Yeosu & Onsan - The First ISCC+ certified sites in APAC in Monomers Division
Yeosu and Onsan sites in Korea received the first ISCC+ certification in Asia-Pacific in Monomers division on their products - MDI, TDI, adipic acid and PA 6.6 in February 2023.
ISCC+ certification is a globally recognized sustainability certification system covering all sustainable raw materials, including agricultural and forestry biomass, bio-based raw materials, and renewable energy. The certification is widely used in various industries such as textiles, packaging, automotive, construction, and white goods.
These certifications of two major production sites in Korea show BASF's deep commitment to enabling our customers to grow their businesses sustainably.
Especially, the Onsan site now is fully capable of offering BMB & ChemCycling® products and has already processed the first customer order. BASF in Korea is expected to reach net zero CO2 emissions for both adipic acid and PA 6.6 produced in Korea by the end of 2024 and 2027 respectively.
The first batch of bio-mass balanced adipic acid has set off from the Onsan site to customers
More and more customers are willing to join the journey towards low-PCF(low product carbon footprint) and collaborate to develop sustainable products. BASF will continue to expand its innovative and climate-friendly product for its customers!
NAS® batteries: Innovative renewable energy solution
BASF is transforming our energy management system in several ways to achieve net zero. To accomplish this goal, we want to expand renewable energy sources such as solar and wind power. However, renewable energy is highly dependent on weather conditions, therefore, it is difficult to predict and unable to obtain steady power. But an energy storage system can help to overcome the limitations!
An energy storage system helps a stable supply of renewable energy by pre-storing that is difficult to produce at the desired time and using the energy when needed. NAS batteries (sodium-sulfur stationary batteries) are energy storage systems. These can store electricity generated by solar or wind power plants, and surplus energy until needed.
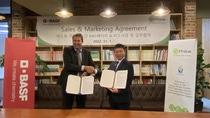%20x%20G-philos.jpg)
MoU signed with G-Philos to collaborate on developing NAS batteries from BASF and power conversion systems (PCS)
BASF Stationary Energy Storage GmbH (BSES), a wholly owned subsidiary of BASF SE, and G-Philos, Korea’s leader in power-to-gas (P2G) technology started to work together in 2020 when a NAS battery system was deployed in a demonstration P2G project implemented by G-Philos in collaboration with Korea Midland Power (KOMIPO) at Sangmyung Wind Farm, Jeju Island, South Korea. In this project, the NAS battery serves as an energy buffer between wind turbines and electrolyzers to ensure stable hydrogen production from wind power despite the fluctuating nature of wind.
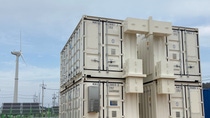
G-Philos installed a NAS battery system (5.8MWh) at New Energy Research Institute in Naju, Jeollanam-do
In addition, in February 2023, BASF and G-Philos completed the commissioning of 1MW/5.8MWh NAS battery system at the Korea Electric Power Corporation (KEPCO) site in Naju, Jeollanam-do. It is expected to make a great contribution to domestic battery storage system research, as the second energy storage system in Korea following the Sangmyeong Wind Farm project in Jeju.
As renewable energy storage, BASF's NAS battery systems will be applied in a lot more applications in the future to help the transition to green energy and reduce carbon emissions!
NAS battery system, a high-capacity long-cycle energy storage, will be the important solution for climate protection.
OASE® blue – Carbon Capture and Strage Solution
The global trend to achieve carbon neutrality by 2050 has brought CCS (Carbon Capture and Storage) technology back into the limelight as a solution that can capture and store CO2 emitted into the atmosphere from production activities.
Recently, BASF has been collaborating in many CCS projects with Korean companies to help curb carbon emissions in Korea through our proprietary CCS solution and pursuing climate neutrality together.
Our CCS solution OASE® blue uses liquid sorbents to specifically target and collect CO2 from exhaust fumes, contributing to carbon neutrality efforts. We also provide optimization solutions for plant operation so that our clients can leverage this technology to maximize efficiency gains as well. For example, BASF’s digital solution OASE® digilab provides continued monitoring services of gas treatment plants and can analyze the components of gas in a matter of seconds.
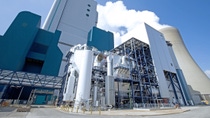
The captured carbon can be used for making dry ice, CO2 welding in shipbuilding, producing biofuels that use microalgae, and synthesizing proteins. This is the circular economy that BASF envisions.
MoU signed with Samsung Heavy Industries to collaborate on developing Onboard Carbon Capture Storage (OCCS)
MoU signed with GS Engineering & Construction to develop modular solutions for carbon capture
Read more about OASE® blue
OASE® blue, your trusted partner in achieving carbon neutrality in Korea!
ecovio® - Soil-biodegradable plastic mulch film
Agricultural mulch films are plastic (PE) films that are used as a surface barrier to modify soil temperature, conserve soil moisture, and reduce weeds. Every year at least 50,000 tons of mulch film are used to grow crops in Korea. Where do these films end up?
The conventional plastic mulch film options require collection after use for films to be recycled. However, most films are not recycled properly and are instead incinerated, releasing carbon into the air and triggering white pollution (pollution that comes from the use of various types of chemical packaging, such as vinyl and polystyrene).
Transforming visions into realities
What if these mulch films could naturally decompose, eliminating the hassle of recovering each sheet of film and providing added agricultural benefits when turned into compost?
This was the thought development process behind ecovio® - an environmentally-friendly, biodegradable film. The diverse range of bio-based content in this high-quality, multipurpose soil-biodegradable plastic means that you can plow the field without collecting the film, and it will compost without polluting the soil. In addition, it provides an innovative and economical solution to the challenges faced by aging rural populations, as it doesn’t require additional manual labor needed to collect used mulch films.
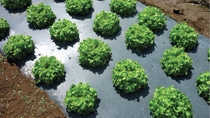
A green and economical compostable solution that doesn’t require collection after use
One step ahead together
The Korean mulch film market is a 50,000-ton market, large enough to cover 250,000 hectares of agricultural land. Since 2017, BASF has been closely working with two local partners in Korea to help fulfil this extensive demand by developing ecovio®. Tests conducted in 2018 showed that decomposition only takes three to four months and that the film does not damage the quality of the crops. Currently, roughly 1,000 tons of ecovio® mulch films are used by farmers in Gangwon-do, Chungcheong-do, and Jeolla-do to grow sweet potatoes and maize. We aim to supply 10,000 tons of ecovio® mulch films, enough span across 50,000 hectares of farmland.
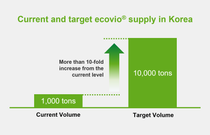
In 2019, ecovio® was awarded the KGCCI Innovation Award (hosted by the Korean-German Chamber of Commerce and Industry) in the sustainability category in recognition of its sustainability and eco-friendly nature in addition to exceptional product quality.
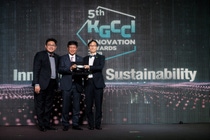
In 2019, ecovio® was awarded the KGCCI Innovation Award (hosted by the Korean-German Chamber of Commerce and Industry) in the sustainability category
Moving forward, BASF in Korea will continue to strengthen and expand innovative business models in various Korean industries, encompassing agricultural mulch films and packaging for food and distribution.
Find out how BASF is changing to protect the climate