Polyamide-6 powder opens a new era in 3D printing
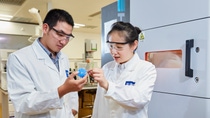
In June 2016, aviation giant Airbus launched Thor (Test of High-tech Objectives in Reality), the world’s first drone made almost entirely from 3D-printed parts. This quick-to-assemble and extremely light (3.96 meters and 20.8 kilograms) aircraft was introduced to the public at the last Berlin Air Show.
With 3D printing, manufacturing can now be more versatile, economical, energy-saving and efficient.
In China, Mr. Liu, Engine Intake and Exhaust Engineer from Pan Asia Technical Automotive Center (PATAC), a joint venture between General Motors and Shanghai Automotive Industry Corporation Motor (SAIC Motor), has been anticipating the industrial applications of 3D printing and the considerable benefits that come along with it. Over the last few years, Mr. Liu has asked his suppliers if they could provide a 3D printing prototype of the intake manifold for the powertrain R&D project that he is in charge of. Gradually, it has become his habit to try to get answers from industry players and partners, but unfortunately without much luck.
At the end of 2014, at an internal workshop co-organized by PATAC and BASF, Mr. Liu by chance sat beside Dr. Dirk Simon, Business Director Innovation Business Unit 3D printing, BASF. This time, when the same question was brought up, he received a different answer: the BASF 3D printing team based in Germany would be delighted to develop a new material for PATAC to meet the experiment requirements of R&D of the powertrain.
In the following year, through close communication and international cooperation, BASF successfully launched 3D printing engine components made of the new polyamide-6 powder in one shot. Enabled by the new technologies provided by BASF and its partner companies, the PATAC team made it possible to successfully complete the process from 3D printing to testing and adjustment of the key components, significantly shortening the development cycle.
It is made possible by the solution for 3D parts printed by selective laser sintering (SLS) co-developed by BASF and Farsoon Hi-Tech, a manufacturer of SLS and melting to develop integral solutions for 3D printing, in 2015.
“The new polyamide-6 powder developed by BASF is the first raw material that made 3D printing parts, which were successfully used in engine testing, possible,” said Mr. Liu. “3D printing components made of PA6 powder could not only carry out product functions, but also shorten the development cycle, save cost and meet the customized requirements of small volume production.”
Today, many plastic parts are produced through injection molding, which is fast and cost-efficient for production of 100,000 parts per year. However, the investment into an injection molding tool makes the production of for instance 10,000 parts per year very expensive. In the development process of products the tooling costs are already avoided by using 3D printing for prototypes.
In addition, individually shaped plastic parts manufactured by 3D printing techniques are gaining increasing prominence in industry with decisive advantages: they enable the production of complex parts, allow individual designs and help lower costs in small scale production; development cycles can be vastly accelerated. Materials currently offered in the market do not satisfy the high requirements for industrial applications for functional components. These requirements include, for example, better material stability under high temperature conditions, and mechanical and chemical stress tolerances.
“BASF will further cooperate with global partners and customers and provide the best solution for this growing market of 3D printing.”
Dr. Dirk Simon, Business Director, Innovation Business Unit 3D printing, BASF
The new polyamide-6 powder that BASF developed for the SLS process is a comprehensive system solution for reliable sintering to build complex parts with better heat distortion temperature (HDT) properties for functional prototyping and production. It can be adapted with partners and customers of BASF for specific applications. Objects made of these innovative materials are distinguished by higher strength and heat-distortion stability than objects made of the previously used polyamide 12. Besides, BASF’s PA6 powder shows good recycling properties: powder not sintered in the production process can be reused to a high degree.
SLS is one of the layer-by-layer additive manufacturing methods used today: following a 3D blueprint, a laser draws the shape of an object in a powder such as polyamide. The material powder hit by the laser beam melts and forms the desired 3D object layer by layer.
The French cloud 3D printing provider Sculpteo lately released a report, The State of 3D Printing 2016, showing that SLS is the top 3D printing technology (38%), and polyamide is the top 3D printing material. Other materials include resins (26%), metals (23%), sandstones (13%) and wax (8%)
Dr. Simon explained that the successful launch of the 3D printing solution mainly relied on three key factors:
1. Open System
Most 3D printer suppliers today offer closed systems, which means that the operator can only use the materials supplied by the specific 3D printer supplier. This limits innovation and competitiveness. BASF and Farsoon share the opinion that the market will grow much faster with open business models. The R&D team did not confine themselves in the labs during the development of the new PA6 powder. They had in-depth cooperation with Chinese customers and conducted 29 trials enabled by overseas travel between Germany and China.
Currently, BASF operates Application Technology Labs in Ludwigshafen and Shanghai. It is opening a 3D Printing Application Technology Center in Heidelberg. With its global network and strong research capability, BASF is cooperating with a few customers and developing solutions together to meet their needs.
2. Global Alliance
Developing new materials for the 3D printing process is not a simple task that could be fulfilled alone. BASF has partnered with Farsoon Hi-tech, a manufacturer of SLS and melting to develop integral solutions for 3D printing. These can be tailored to meet a customer’s individual needs. This was recognized as a joint-forces benefit from the complimentary know-how of the parties in material and formulation as well as technology, machinery and services.
This collaboration is open for potential customers to jointly develop solutions for functional applications where materials, equipment and processing are aligned. Customers interested in a solution for a 3D printed part don’t need to worry about receiving all the necessary elements for the solution. They also have the choice to purchase products and services from competition.
3. Broad portfolio and industry insights
As the world’s leading chemical company, BASF has a broad product portfolio and formulation know-how relevant for 3D printing. Moreover, BASF is an established supplier of materials used in traditional manufacturing. It is well positioned to help customers and partners to overcome high barriers for growth with its know-how and industry insights.
3D printing offers unforeseen design options for the aeronautical, automotive, health care, intelligent manufacturing, leisure and sports industries. High-end users of 3D printing rely more on accelerating product development and offering customized products and limited series. BASF sees great potential in it and is working on developing new materials for customers to use in the various processes of additive manufacturing.
“In the next three years, the Innovation Business Unit 3D printing will further cooperate with global partners and customers to discover market trends, incubate market opportunities and accelerate business development to provide the best solution for this growing market,” said Dr. Simon.