Sustainable materials for innovative buildings
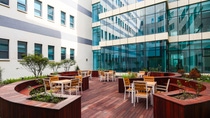
Urbanization makes cities prosper and life more easy than ever before. But buildings, as the main body of a city, are one of the biggest energy guzzlers, accounting for a quarter to a third of total energy consumption. Research by the McKinsey Global Institute shows that four out of five of the most cost-efficient measures to lower greenhouse gas emissions are energy saving measures for buildings.
It is for this reason that the concept of sustainable buildings has come into being as the key to saving energy and reducing emissions for cities, to protect the environment and to promote sustainable development. Building materials play a vital role in increasing energy efficiency and promoting urban sustainable development.
With its own strengths in construction chemicals, BASF actively participates in and contributes to the development of the sustainable construction industry worldwide, committed to creating a sustainable future for our planet. At the 2010 Shanghai World Expo, BASF provided an insulation solution for Hamburg-house, the first passive house in China.
In November 2015, the second phase of the BASF Innovation Campus Asia Pacific (Shanghai) was inaugurated. Using the DGNB1 and LEED2 standards in design, construction and operation, the project has fully leveraged BASF’s innovative construction materials to create a sustainable building at the BASF Greater China headquarters in Pudong.
“The second phase of the BASF Innovation Campus Asia Pacific (Shanghai) adopted a series of cutting-edge construction materials and solutions by BASF, creating an eco-friendly, safe and pleasant working environment for our employees,” said Ma Shouwang, Senior Manager of Industry Team Construction China, BASF.
As roof waterproofing quality impacts the durability of an architectural structure and the life of a building, it is a significant process in construction. BASF’s MasterSeal® waterproofing system does an excellent job on the roofing of the new R&D building in the second phase of BASF Innovation Campus Asia Pacific (Shanghai). MasterSeal® system forms a monolithic membrane that is fully bonded to the roof substrate after curing, protecting the building like a huge umbrella without leakage.
Produced with BASF raw materials, the MasterSeal® spray applied polyurethane waterproofing system was created in an environmentally friendly nature. It has excellent elasticity, UV resistance and weather resistance, and can withstand corrosion and structure movement caused by exposure to bad weather. A building, therefore, will have longer life and lower needs for maintenance. Even when the membrane is damaged somewhere, water will not track underneath and the leak can be quickly found, improving maintenance efficiency and lowering maintenance costs.
Leaking in bathrooms is one of the most common problems found in buildings. The new R&D building use MasterSeal® cementitious waterproofing coating. It adapts to a wet substrate and provides a good interface for tiling and other decorative coatings. It also has the flexibility to resist structure movement caused by temperature changes and other factors. It is ideal for waterproof application in bathrooms, kitchens, balconies and pools, like a reliable dam for the building.
With chemistry labs on the premises, the new R&D building has a special and cautious need for a flooring system. According to Ma, chemistry labs require outstanding performance in resisting corrosive chemicals, impact and wear load. They should also be slip-resistant and easy to clean; a traditional flooring system won’t qualify.
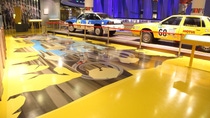
Ucrete®, an industrial flooring system that is more than 40 years old, is popular within the industry. It is often known as “the toughest industrial flooring in the world”. Not only does it meet the above-mentioned criteria but also satisfies all emission requirements for indoor flooring systems in Europe. Ucrete® is durable, environmentally friendly and thus being used on the grounds of the new R&D building.
Moreover, Ucrete® performs brilliantly in slip resistance. Since it does not cause biodegradation or breed bacteria or fungi, it can be as clean as stainless steel. Therefore, the floor of the Pudong Cube Canteen uses Ucrete as it is easy-cleaning, attractive, safe, reliable and comfortable to walk on.
The Ucrete® flooring system has attracted the attention of the food and beverage industry in recent years, in addition to the chemical and pharmaceutical industries. As the food industry requires a clean and germ-free manufacturing environment, chemical substances are often used to clean floors and hot water to kill germs. Traditional floors, as a result, have to be replaced and renovated every year or two.
Ucrete®, with no such worries, has been very important in the food safety system. In China, it has been chosen by well-known companies such as Coca-Cola, Pepsi, Yurun Group, Charoen Pokphand Foods, Nestle Group, Want Want Group, Wanglaoji and Yili. Meanwhile, Ucrete® is highly valued in the pharmaceutical and chemical industries and others that require durable flooring.
The Finestone® wall thermal insulation and finishing system was used on the exterior walls of the second phase of the BASF Innovation Campus Asia Pacific (Shanghai). The multi-layer thermal insulation system is not only highly decorative but is protective with good thermal insulation and weather resistance. In addition to functionality, it comes in a wide range of textures, colors and patterns.
The Finestone® rock wool thermal insulation system is applied to the exterior walls. In winter heat is prevented from moving outward, while in summer heat is shielded from the outside, making the building energy efficient for all seasons with low energy consumption and carbon emissions. This innovative thermal insulation system also meets Grade A fire prevention requirements: it will not combust, even in a fire, making a building much safer.
During the construction process, thermal boards are glued to exterior walls with the Finestone® Adhesive & Base Coat. The product is highly capable of being adhesive, flexible, efficient, air-penetrating and waterproof.
The exterior wall finishing of the Innovation Campus features Finestone@ STONELOOK coating products, which take on a stone-decoration appearance yet lower the consumption on natural resources. It also avoids pollutions to the environment brought by stone processing, and saves a large amount of manpower and facilities that may be needed in stone installation.
The interior walls of the building use the latest Finestone® water-based coating, which is not only anti-bacterial and anti-fungal but also emits zero-VOC (volatile organic compound) and formaldehyde3. It is odorless and environmental friendly, ensuring the health and safety of employees. Moreover, Basotect® acoustic insulation foam should be given credit for the quiet and comfortable environment inside the building since its brilliance in sound absorption and fire resistance improves the acoustic environment inside the rooms.
The R&D building in the second phase of the BASF Innovation Campus Asia Pacific (Shanghai) is the first research laboratory building in China that has been constructed according to the DGNB standard and LEED certified. To be certified as a green building, however, is not the only goal of this project.
According to architect and DGNB auditor Rolf Demmler, Director of SoftGrid (Shanghai) Co, Ltd, the DGNB standard is a tool to optimize the design, construction and operation of a building. It focuses holistically on evaluating the ecological, economic, functional, technological and social performances of a building as its major goal.
“DGNB focuses on the integration and optimization of architectural projects, and prefers balancing among all indexes,” said Demmler. “BASF products are not only outstanding and environmentally friendly but are also equipped with a series of complete and professional systematical documentation, which is extremely helpful to the implementation and application of DGNB certification of the Innovation Campus in Shanghai.”
With a premise that the project is reasonable in budget, achievable in schedule and safe in operation, the second phase of the BASF Innovation Campus Asia Pacific (Shanghai) has optimized ecological performance, achieved a high level of energy saving and environmental protection results and created a comfortable and healthy architectural environment.
The application of BASF building materials, meanwhile, has changed traditional construction methods so that construction efficiency has been greatly improved and post-phase maintenance costs are reduced. In terms of comprehensive performance and cost perspectives, the second phase of the BASF Innovation Campus Asia Pacific (Shanghai) features more advantages than ordinary buildings.
While the Ucrete® flooring system costs more than the traditional solution, for example, it lasts for at least 20 years, over 5 times that of the latter. The total cost, therefore, is significantly lowered.
“Thanks to a series of advanced BASF chemical building materials solutions, energy consumption and carbon emission have been greatly reduced,” said Ma. “The second phase of the BASF Innovation Campus Asia Pacific (Shanghai) is a great example of BASF successfully balancing the economic benefits and social and environmental responsibilities.”
Endnotes:
1 DGNB (Deutsche Gesellschaft für Nachhaltiges Bauen e.V., i.e. German Sustainable Building Council) is a system describing and evaluating building sustainability developed jointly by German Federal Ministry of Transport, Construction and Urban Development.
2 LEED (Leadership in Energy and Environmental Design) is a green building certification program established and implemented by the United States Green Building Council.
3 Zero-VOC and formaldehyde: no volatile organic compound or free formaldehyde is tested based on the standard of GB18582-2008.