Change for climate
Grüner Motor für die Chemie
Steamcracker sind die Motoren im Herzen der chemischen Industrie. Gasbetriebene Hochtemperaturöfen sind für die Basischemie unverzichtbar. Allerdings ist der Prozess energieintensiv und emittiert erhebliche Mengen an CO2. Um sowohl beim Klimawandel als auch bei der Energietransformation voranzugehen, begannen BASF, Sabic und Linde 2022 mit dem Bau der weltweit ersten Demonstrationsanlage für großtechnisch, elektrisch beheizte Steamcracker-Öfen (eFurnace). Im April 2024 feierten die drei Unternehmen die Inbetriebnahme der Demonstrationsanlage. Unser Ziel in diesem Projekt: Die CO2-Emissionen eines der energieintensivsten Produktionsprozesse in der chemischen Industrie, um mindestens 90 % im Vergleich zu heute eingesetzten Technologien zu reduzieren.
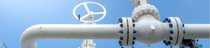
Die Idee: Veränderungen vorantreiben
Viele Alltagsprodukte werden aus Rohstoffen hergestellt, die ohne den Steamcracker und dessen Hochtemperarturöfen, die typischerweise bei extrem hohen Temperaturen von etwa 850 °C betrieben werden, nicht existieren würden. Zu Beginn der chemischen Wertschöpfungskette, werden langkettige Kohlenwasserstoffe (Naphtha, Rohbenzin) in diesen Öfen aufgespalten. Der Prozess produziert Olefine und Aromaten – Chemikalien, die die Grundlage für viele Produkte bilden, darunter Vitamine, Lösemittel, Spezialchemikalien, Kunststoffe und Pharmazeutika.
Heutzutage werden die Steamcracker-Öfen mit fossilen Brennstoffen betrieben. Die Elektrifizierung der Öfen könnte das Herzstück der weltweiten chemischen Industrie verändern.
Die Grundlage: Naphtha
Naphtha wird aus Rohöl gewonnen. Es wird für die Benzinproduktion verwendet, bildet aber auch die Grundlage für Ethylen und Propylen, Benzol, Toluol und Xylol. Zusammen mit Methanol und Ammoniak bilden sie die sieben Grundchemikalien, auf denen fast die gesamte industrielle organische Chemie basiert.
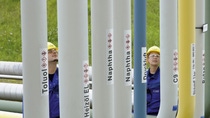
Der Verbundstandort von BASF in Ludwigshafen hat einen eigenen Hafen. Von verschiedenen Anlegestellen aus werden die Grundstoffe für die chemische Produktion wie Naphtha, Methanol oder komprimierte Flüssiggase über Rohrleitungen direkt zu den Produktionsanlagen oder in Lagertanks transportiert.
Die Mission: das Wesentliche überdenken
BASF hat sich ehrgeizige Ziele gesetzt und ist bestrebt, bis 2050 weltweit Netto-Null-CO2-Emissionen1 zu erreichen. Um diesen Meilenstein zu erreichen, ist die Umstellung der chemischen Produktion auf erneuerbare Energiequellen unerlässlich. Das eFurnace-Projekt wird einen großen Einfluss auf den Weg zur Klimaneutralität haben. Die Demonstrationsanlage soll zeigen, dass im Vergleich zu herkömmlichen Steamcracker-Öfen die CO2-Emissionen um mindestens 90 % reduziert werden können.
Erfahren Sie, wie wir Emissionen reduzieren
Erfahren Sie mehr über unsere Klimaschutzziele
1 Das Ziel umfasst Scope 1, Scope 2 und Scope 3.1-Emissionen. Andere Treibhausgase werden gemäß dem Treibhausgasprotokoll in CO2-Äquivalente umgewandelt.
Der Aufbau: Integration des Unmöglichen
Der Bau der Demonstrationsanlage begann 2022 und wurde im April 2024 abgeschlossen. Die Demonstrationsanlage soll die kontinuierliche Olefinproduktion mit erneuerbarer Energie als Wärmequelle unter Beweis stellen. Die Anlage ist so konzipiert, dass zwei Heizkonzepte parallel getestet werden können: Bei der direkten Beheizung wird elektrischer Strom direkt an die Rohre im Reaktor angelegt; die indirekte Beheizung nutzt die Strahlungswärme von Heizelementen, die um die Rohre angeordnet sind.
Der Prototyp wird vollständig in einen der beiden bestehenden Steamcracker am BASF Standort in Ludwigshafen integriert. Darüber hinaus betreibt BASF Steamcracker in Port Arthur (Texas), Antwerpen (Belgien) und Nanjing (China).
Sehen Sie sich das Video über die letzten Schritte auf der eFurnace-Baustelle an.
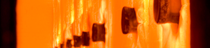
Das Ziel: Pilotprojekt für die Transformation
Die Steamcracker-Ofen-Demonstrationsanlage verarbeitet etwa vier Tonnen Kohlenwasserstoff pro Stunde. Um die langen Kohlenstoffketten in Olefine und Aromaten aufzuspalten, wird die Anlage etwa sechs Megawatt erneuerbare Energie aus Wind-, Solar- und Wasserkraft nutzen.
Dies veranschaulicht die erhebliche Energie, die für den Betrieb von Steamcrackern benötigt wird, und die potenziellen CO2-Einsparungen die erzielt werden könnten, wenn dieses Pilotprojekt erfolgreich ist. Wenn alle Steamcracker weltweit mit Strom aus erneuerbaren Energiequellen betrieben würden, hätte dies erhebliche Auswirkungen auf die Nachfrage nach grüner Energie in der chemischen Industrie.
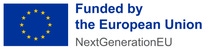
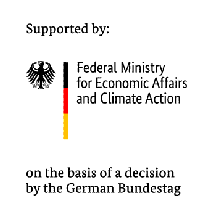
Die Zukunft der grünen Chemie: Finanzierung von Veränderungen
Das Bundesministerium für Wirtschaft und Klimaschutz hat das enorme Potenzial des Projekts erkannt – die Entwicklung der Demonstrationsanlage wird mit 14,8 Millionen Euro durch das Förderprogramm „Dekarbonisierung in der Industrie“ unterstützt. Ein Programm, das energieintensive Industrien in Deutschland bei ihren Bemühungen zur CO2-Neutralität unterstützt. Das Projekt wird ebenfalls von der Europäischen Union im Rahmen des NextGenerationEU-Programms finanziert.
BASFs Mission, Netto-Null-CO2-Emissionen und die Elektrifizierung des enorm energieintensiven Steamcrackers zu erreichen, ist ein wichtiger Meilenstein auf unserer Transformationsreise.
BASF Verbund: effiziente Ressourcennutzung
Verbund bedeutet im Wesentlichen, verbunden zu sein. Bei BASF ist Nachhaltigkeit bereits lebendige Realität. An unseren einzigartigen Verbundstandorten sind Produktionsanlagen, Energieströme, Logistik und Infrastruktur auf intelligente Weise miteinander verbunden, sodass wir Energie effizienter nutzen und Ressourcen sparen können. Nebenprodukte aus einem Prozess werden als Rohstoffe für andere verwendet. Dies reduziert nicht nur die Emissionen, sondern senkt auch die Logistikkosten. Intelligente Vernetzung ermöglicht auch eine optimale Energieversorgung an unseren Standorten. Beispielsweise wird die Abwärme aus dem Produktionsprozess in einer Anlage als Energie in anderen Anlagen genutzt.
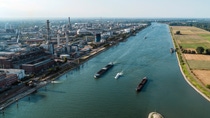
BASF verfügt über sechs Verbundstandorte in Europa, Nordamerika und Asien. Sie sind unsere Herzstücke und verantwortlich für mehr als die Hälfte aller BASF-Produkte. BASF betreibt darüber hinaus 233 weitere Produktionsstätten weltweit.
Erfahren Sie mehr über grüne Chemie bei BASF:
Gefördert von der Europäischen Union – NextGenerationEU. Die geäußerten Ansichten und Meinungen sind ausschließlich die des Autors und spiegeln nicht notwendigerweise die Ansichten der Europäischen Union oder der Europäischen Kommission wider. Weder die Europäische Union noch die Europäische Kommission können für sie verantwortlich gemacht werden.