Factbook
BASF Verbund
The Verbund concept is one of BASF’s key strengths, enabling us to intelligently link and steer our plants and permitting resource-efficient, CO2-optimized and reliably managed production.
BASF currently operates six Verbund sites worldwide: two in Europe, two in North America and two in Asia. Our Verbund site in Ludwigshafen, Germany, is the world’s largest chemical complex owned by a single company that was developed as an integrated network. We are building a seventh Verbund site in Zhanjiang, in the Chinese province of Guangdong.
BASF Verbund sites worldwide
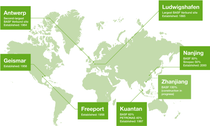
The Verbund system creates efficient value chains that extend from basic chemicals all the way to industrial and final consumer products. In this system, chemical processes make use of energy more efficiently, achieve higher product yields and conserve resources. By-products of one process are used as starting materials for other processes. This saves raw materials and energy, avoids emissions, lowers logistics costs and leverages synergies. BASF operates 235 production sites worldwide, but the six Verbund sites produce more than 50% of our volumes. This is a testament to the importance and strength of the Verbund concept within BASF.