Factbook
Intermediates
With more than 600 products in its portfolio, in particular amines, diols, polyalcohols, acids and specialties, the Intermediates division offers innovative and sustainable solutions for a wide range of industries – from coatings and plastics to pharmaceuticals and crop protection. The division focuses primarily on the C1 and C2 value chains. Its products are typically used by customers as precursors for their downstream chemicals, and the products are also widely used for BASF’s own downstream production. The Intermediates division is a global leader in sustainable chemical intermediates, which can support our customers in achieving their sustainability goals, for instance with our OASE® gas treatment solutions as well as LowPCF and ZeroPCF products.
Sales by direct customer industry 2024
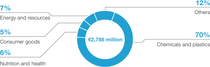
Portfolio
Acetylenics and carbonyl derivatives
These specialty intermediates are based on raw materials from BASF’s Verbund, such as acetylene and chlorine. Among the acetylene derivatives are vinyl monomers, acetylenic alcohols and higher alkylpyrrolidones. Chlorine-based intermediates include acid chlorides and chloroformates. Further specialty intermediates are glyoxal and imidazoles, cyclododecanone, 2-mercaptoethanol and triphenylphosphine. The products serve as building blocks for crop protection agents and pharmaceuticals or as monomers and performance additives for polymers, coatings and printing inks.
Acids and polyalcohols
BASF is the world’s leading manufacturer of polyalcohols, such as neopentyl glycol (NPG) and 1,6 hexanediol (HDO), and carboxylic acids, such as formic and propionic acid. Carboxylic acids are used as preservatives for the feed and food industries, as auxiliaries for textile and leather applications and as deicing agents. The portfolio also includes higher carboxylic acids such as 2-ethylhexanoic acid and isononanoic acid (iNA), which are primarily utilized in synthetic lubricants, paint dryer and PVC plasticizer applications. Polyalcohols are mainly offered for the production of a wide range of coatings.
Amines
With about 300 different amines, we have the world’s most diverse portfolio of this type of chemical intermediate. Along with alkyl-, alkanol-, alkoxyalkylamines and ethyleneamines, we offer heterocyclic and aromatic as well as specialty amines. The range is completed by a portfolio of chiral amines of high optical and chemical purity. The versatile products are used mainly to manufacture process chemicals, pharmaceuticals and crop protection agents, as well as cosmetic products and detergents. They also serve to produce coatings, specialty plastics, composites and specialty fibers.
Butanediol and its derivatives
BASF is among the world’s largest manufacturers of 1,4-butanediol, which is a chemical building block for products such as polyesters and polyurethanes. Its derivatives are used to manufacture products ranging from fibers to paints, pharmaceuticals and lithium-ion batteries, and include N-methylpyrrolidone, tetrahydrofuran (THF) and PolyTHF®.
Innovation
We consistently align our innovation activities with the needs of our customers. As sustainability is the most important driver of innovation in many of our customer segments, we strive to make our product portfolio more sustainable and thus enable our customers to better achieve their sustainability goals.
We have launched a number of our chemical intermediates as “LowPCF” products globally. This suffix denotes the low product carbon footprint (PCF) relative to that of comparable products available on the market. Our range of LowPCF products currently consists of formic acid (FA), propionic acid (PA), 1,6-hexanediol (HDO®) and NPG.
In addition, we have been globally offering NPG and PA produced at our Ludwigshafen Verbund site with the suffix “ZeroPCF.” We achieve this by using renewable raw materials in our Production Verbund via our biomass balance (BMB)1 approach. We additionally use renewable energy in the production of NPG.
As drop-in solutions, our LowPCF and ZeroPCF products have the identical quality and properties as standard products. As a result, our customers can use them without having to adapt their existing processes. Customers can easily and efficiently reduce their Scope 3 emissions from purchased goods and increase the share of renewable raw materials in the value chain, thus contributing to the transition to a circular economy.
1 The biomass balance approach allows fossil fuels to be replaced by renewable raw materials in BASF’s Production Verbund. The amount of renewable feedstock is allocated to specific products using a third party-verified certification method. For more information on the mass balance approach, see basf.com/massbalance
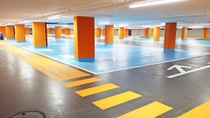
Baxxodur® EC 151 for ultra-low VOC flooring applications
BASF and Sika have jointly developed a new amine building block for curing epoxy resins, which is now commercially available under BASF’s Baxxodur® EC 151 brand. This new development is particularly interesting for flooring applications, for example, in production plants, storage and assembly halls, as well as parking decks. Baxxodur EC 151 gives epoxy resin flooring solutions a low viscosity and optimum flow properties. As a result, the coatings are easy to apply and spread evenly. Compared to conventional hardeners, significantly less thinner is required, and up to 90% less volatile organic compounds (VOCs) are released.1 Baxxodur EC 151 thus enables the production of ultra-low VOC formulations.
1 Based on emission measurements commissioned by Sika according to AgBB, Emicode M1 and LEED v4 with selected Sika products containing Baxxodur® EC 151, such as Sikafloor®-2640, as compared to equivalent products without Baxxodur® EC 151.
Market position and main competitors
The Intermediates division holds one of the top three market positions in all strategic business areas in which it is active.
The main competitors (alphabetical order) include Dairen, Dow, Eastman, Huntsman, Luxi, LyondellBasell and Wanhua.
Focus of research and development
The main aim of process innovation is to optimize existing production technologies and develop new, highly efficient processes that offer significant sustainability contributions and cost benefits.
Acquisitions/JVs/investments
From 2022 onward
Product group | Description | Year |
Alkylethanolamines | Capacity expansion in Antwerp, Belgium | 2024 |
Chlorofomates/acid chlorides | Modernization in Ludwigshafen, Germany | 2026 |
2-Ethylhexanoic acid | Capacity expansion in Kuantan, Malaysia1 | 2024 |
Neopentyl glycol | New plant in Zhanjiang, China | 2025 |
Propionic acid/ethanolamines/ ethyleneamines | Capacity expansion in Nanjing, China2 | 2023 |
1 Operated in a fully consolidated joint venture with PETRONAS Chemicals Group Berhad
2 Operated in a joint venture with Sinopec; the startup of the plant expansions for ethanolamines and ethyleneamines took place in early 2024.
Divestitures/shutdowns
From 2022 onward
Product group | Description | Year |
Adipic acid, cyclododecanone (CDon) and cyclopentanone (CPon) | Closure of plants in Ludwigshafen, Germany | 2025 |
o-Nitrotoluene (oNT) and o-toluidine (oT) | Closure of plants in Schwarzheide, Germany | 2025 |
1,4-Butanediol (BDO) | Divestiture of shares in joint ventures in Korla, China, to Verde Chemical Singapore Pte. Ltd. | 2025 |
Major nameplate capacities of BASF1
Thousand metric tons per year
Product group | Capacity |
Alkylamines | 250 |
Butanediol equivalents | 550 |
Ethanolamines and derivatives | 530 |
Formic acid | 305 |
Neopentyl glycol (Neol®) | 255 |
PolyTHF® | 350 |
Propionic acid | 220 |
Specialty amines | >100 |
1 All capacities are included at 100%, including plants belonging to joint operations and joint ventures.