Digitalization
Manufacturing
We are increasing the effectiveness of our plants and the efficiency of our production processes through the use of digital technologies and data. With mobile devices, we have access to information relevant to our daily work. The tight integration of production and business processes allows us to make better and faster decisions.
Augmented Reality
The “Augmented Reality” application supports employees at our plants in their daily tasks. Through the application, they have direct and quick access to necessary information via especially equipped mobile devices, such as tablets or smartphones. This enables us to increase the efficiency of our processes and ensure a more sustainable knowledge transfer.
Predictive Maintenance
The “Predictive Maintenance” application aims to predict the optimal time to carry out maintenance measures in order to reduce unplanned repairs and failures and to optimize the coordination of maintenance and production processes.
The application is based on the forecast of the functional state of critical parts and components in production plants, such as compressors or heat exchangers. With the help of sensors, live data on the operating conditions is available and modeled and then evaluated using a special analysis software which also takes historical process data into account.
Critical Equipment & Process Units e.g.:
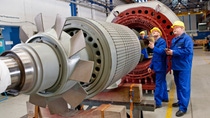
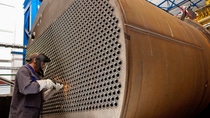
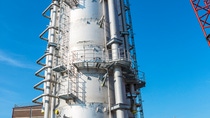
Electricity and steam generation in power plant 4.0
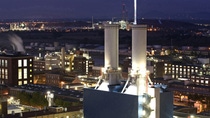
Our Ludwigshafen Verbund needs roughly 20 million metric tons of steam per year, which are generated by the production plants and the site's three power plants. In addition, the power plants produce the majority of electricity needed at the site – and sometimes more than is required, so that electricity can be fed into the public grid.
However, electricity is a complex business as market prices fluctuate every 15 minutes. Computer programs help to buy and sell at the best times. For this, however, a precise forecast is required as to how much steam and waste heat the production plants supply at the site, how much steam the power plants have to contribute and how much electricity is needed. This also fluctuates depending on the time of year, the weather and the economic conditions.
To date, the total requirements have been determined manually combined individual forecasts of the plants. A new statistical model, based on large amounts of data, now provides even more precise calculations: The software takes into account, among other things, historical and up-to-date information on production shutdowns, weather data and economic indices. The program searches for relationships and establishes connections with the energy demand.
This has been very successful: The forecast for steam demand has already improved by up to 60 percent. The former procedure will now be gradually replaced and applied to other areas. The new program supports us also in electricity trading to make better price forecasts.