Who we are
Safety Assessment and Testing
At the Safety Engineering Laboratory of BASF SE, we deliver high-quality data and expert analysis to support the development of robust safety concepts covering:
-
Ignition processes, including electrostatics
-
Explosion behaviour of gases and dusts
-
Thermal process safety
-
REACH and transport classification
With our ISO/IEC17025 accreditation (for the scope of accreditation listed in the annex to our certificate PL-14121-03-00) and GLP/ISO9001 certification, we provide precise measurements and safety evaluations not only for BASF but also for external customers seeking reliable, science-based safety solutions, and with our unique facilities we also offer a wide range of tailor-made testing.
Service
Consultation regarding test methods
Electrostatic Properties
Tests in the field of electrostatics provide information about the occurrence and type of electrostatic charges in the process, as well as the conductivity or insulating properties of materials, equipment, and personal protective equipment. This information is essential for evaluating ignition sources and assessing the behavior of bulk materials or the use of equipment, packaging materials, etc., in explosion-prone areas.
Surface resistance
The surface resistance provides information about the electrical resistance on the surfaces of products and materials. Additionally, surface resistance allows for tracking changes in resistance due to external influences. The following methods for determination are available:
-
DIN EN 62631-3-2, solid, electrically insulating materials
-
DIN EN 1149-1, protective clothing
Volume resistance
The volume resistance is a part of the insulation resistance. The specific volume resistance can be helpful in selecting an insulating material for a specific application. The variation of specific volume resistance with temperature and humidity can be significant and must be known during the design phase concerning operating conditions. The following methods for determination for different applications are available:
-
DIN EN 62631-3-1, electrically insulating materials
-
DIN EN 1149-2, protective clothing
-
based on DIN EN 61340-2-3, protective gloves
-
DIN EN 63140-2-3, protective gloves
-
earth leakage resistance according to IEC 61 340-2-3
Electrical conductivity of liquids
The parameter 'electrical conductivity' is used for the classification of liquids. The following methods for determination are available:
-
in accordance with DIN 51 412, Part 1, mineral oil products
-
DIN EN 27 888, Water
-
in accordance with DIN EN 60 243-2, forward voltage
Resistance, Resistivity
The parameter serves as a basis for assessing the behavior of dust accumulations or the usability of equipment and/or materials in explosion-prone areas
-
Dust accumulations in accordance with DIN EN ISO/IEC 80079-20-2
-
Rubber and plastic hoses in accordance with DIN EN ISO 8031
-
Flexible bulk materials according to DIN EN 61340-4-4 VDE 0300-4-4
-
Permittivity number according to IEC 60247
Physical Properties
In our portfolio, we offer the determination of safety-relevant physical properties
Heat capcity
The heat capacity of a substance or mixture is the change in its enthalpy (at constant pressure) or its internal energy (at constant volume) with temperature. The specific heat capacity is the heat capacity per unit mass or per mole. The parameter can be determined using the following methods:
-
using Differential Scanning Calorimetry according to DIN 51007
-
using a reaction calorimeter (CPA 202)
-
using Calvet calorimetry (C80)
-
using titration calorimetry
Penetration according to GGVSEB/ADR Annex A Part 2, Chapter 2.3.4
This test is necessary to differentiate flammable liquids from flammable solid or paste-like substances in accordance with the regulation on flammable liquids (VbF) and to determine the flow behavior of liquid and viscous mixtures of Class 3, as well as paste-like substances of Class 4.1 (GGVS/ADR).
Thermal conductivity using Hot Disc Method according to DIN EN ISO 22007-2 (only solids)
The Hotdisk is a transient measurement method for determining the thermal conductivity of solids and powder samples with isotropic (direction-independent) heat transport properties. Thermal conductivity measures the ability to transport heat within a substance (solid, liquid, or gas) (synonyms: thermal conductivity coefficient, thermal conductivity)
Particle size distribution
The particle size distribution indicates the proportions of the various particle size fractions present in a solid sample. The following methods are available for determining the particle size distribution:
-
using wet cell method (GLP)
-
using the Hartmann tube method
Reduction/Oxidation: Chemical Incompatibility (GLP)
According to OPPTS 830.6314, it is tested whether a hazardous reaction occurs when the test substance comes into contact with reducing or oxidizing agents, components from fire extinguishers, or common solvents. Significant temperature increases, the generation of gases and vapors, splashes, and the formation of flames are potential hazards that need to be evaluated. Information on the reductive and oxidative properties of the test substance is required by 40 CFR §158 for the registration of end products
Burning Behavior
These tests can determine the bruning behavior of organic and inorganic substances and/or mixtures in liquid or solid form. The information forms the basis for developing safety concepts or classifying the substance and/or mixture according to REACH and/or transport regulations.
Burning Behavior according to VDI 2263
The burning number (BN) is a criterion for the spread of a fire following the localized impact of a sufficiently strong ignition source, making it an important parameter for the burning behavior of solids and the subsequent fire protection concept.
Bunring rate Test according to UN Test N.1 (GLP)
The burning rate describes the maximum propagation speed of the combustion zone in solids and is a criterion for burning behavior. It is relevant for classification according to UN transport regulations and hazardous materials regulations
Oxidizing Properties according to UN Test O.1, O.2 , O.3 (GLP)
The tests are to be conducted to determine the oxidation potential of a solid or liquid substance. They serve for classification according to hazardous materials and substances regulations. In general, a solid or liquid is considered oxidizing if the test substance exhibits a higher oxidation potential in a mixture with cellulose than a defined reference mixture. The classification of liquids is carried out according to UN Test O.2. Solids are classified according to UN Test O.3.
Flash Point
The flash point is the lowest temperature of a flammable liquid (boundary condition: the environment is air at ambient pressure) at which the vapor pressure becomes high enough to create an explosive vapor/air mixture above the liquid for the first time. This is demonstrated by an ignition test using a methane/air flame. The flash point is a central parameter for assessing the fire and explosion hazards that can occur when handling liquids with exposure to air. It serves as the basis for the classification and labeling of flammable liquids and is part of many product specifications. We offer flash point determination according to the following standards:
-
DIN 51 755 (GLP)
-
DIN EN ISO 2719 (GLP)
-
DIN EN ISO 1523 (GLP)
-
DIN EN ISO 2592
-
DIN EN ISO 3679(GLP)
-
DIN EN ISO 13736
Sustained combustibility according to UN Test L.2 (GLP)
The method is used to determine whether a substance burns self-sustainingly, thus classifying it as a Class 3 substance.
Smoldering point of bulk material according to VDI 2263
The smoldering point is the lowest temperature at which a bulk material generates smoldering gases in such quantities or releases flammable gases through off-gassing in such amounts that explosive combustible gas/air mixtures can form in the vicinity of the substance, which can be ignited by an ignition source, leading to an explosion
Explosive behavior of gases, vapors, and dusts
These tests are conducted to determine explosion-related safety characteristics for the development of explosion protection concepts and the determination of explosion diagrams, as well as explosion limits of dust/air mixtures or gases/vapors..
Limiting Oxidant Concentration of gases and vapours in closed vessels according to EN 1839
Determination of the oxidizing gas boundary concentration of a three-component system of the type fuel/oxidizing gas/inert gas. The measurement is conducted in a closed, pressure-resistant container in accordance with the standard DIN EN 1839, Method B.
Explosion diagram of gases/vapours in closed vessels according to EN 1839
Determination of the explosion diagram of a three-component system of the type fuel/oxidizing gas/inert gas. The measurement is conducted in a closed, pressure-resistant container in accordance with DIN EN 1839, Method B.
Explosion characteristics (pmax, KG) of gases/vapours in closed vessels according to DIN EN 15967
Determination of the explosion characteristics (maximum explosion pressure pmax and maximum rate of pressure rise KG) of various flammable gases and flammable vapors in a mixture with an oxidizing gas/inert gas mixture of any (but constant during the measurement) composition. The measurement is conducted in a closed, pressure-resistant container in accordance with DIN EN 15967.
Explosion points of vapours at ambient pressure according to DIN EN 15794
It is tested in which temperature range vapors over liquids form explosive mixtures with air at normal pressure. The measurement is conducted in accordance with DIN EN 15794 'Determination of Explosion Points of Flammable Liquids'. The explosion points can be determined as follows
-
lower and upper explosion point
-
only lower explosion point
Ignition behavior
These parameters are used to characterize the ignition behavior of gases and vapors on hot surfaces, of deposited dust layers due to oxidative self-heating or spontaneous reactions in air or with water, and of dispersed dust/air mixtures on hot surfaces ignited by released energies, such as electrostatic phenomena. These parameters form a basis for the safe design of processes and are partially relevant for transport classifications and classification according to hazardous materials regulations. The following methods for investigating ignition behavior are offered:
Pyrophoric properties
It is tested whether the test substance possesses pyrophoric properties at room temperature. Substances are considered pyrophoric if they ignite spontaneously in small amounts in air after a short period of time at room temperature.
-
Solids according to UN Test N.2 (GLP)
-
Liquids according to UN Test N.3 (GLP)
Minimum ignition temperature of a dust layer (Smoldering temperature)
The minimum ignition temperature of a dust layer (smoldering temperature) describes the ignition behavior of thin dust layers on hot surfaces. The minimum ignition temperature of a dust layer is the lowest temperature of a heated exposed surface at which deposited dust in a 5 mm thick layer ignites. We conduct the measurement as follows:
-
according to DIN EN ISO/IEC 80079-20-2, Part 8.2
Self-Ignition behaviour of dust accumulations
The self-ignition of dust accumulations occurs as a result of heat release due to an oxidation reaction with atmospheric oxygen. Self-ignition often leads to the formation of smoldering fires. These can occur, for example, during drying processes or storage in silos or similar storage facilities, acting as an ignition source. The self-ignition behavior also influences the transport classification of a bulk material. To characterize the self-ignition behavior of dust accumulations, we offer a wide range of services from simple screening using the Grewer oven test to determining the self-ignition temperature and its volume dependence, as well as standardized testing methods for classification into transport classes according to the UN Manual of Tests and Criteria:
-
Grewer Oven-Test according to VDI 2263 (GLP)
-
according to DIN EN 15188
-
Relative self-ignition temperature according to A.16 (GLP)
-
according to UN Test N.4 (GLP)
Minimum ignition temperature of gases and vapors
Determination of the minimum ignition temperature of gases and vapors in mixtures with air or air/inert gas at ambient pressure. The minimum ignition temperature is the lowest temperature (of a hot surface) at which, under specified test conditions, the ignition of a flammable gas or vapor in a mixture with air or air/inert gas occurs. The measurement is conducted as follows:
-
according to DIN EN ISO/IEC 80079-20-1 (GLP)
-
Minimum ignition energy
The minimum ignition energy is the lowest electrical energy stored in a capacitor that is sufficient, upon discharge, to ignite the most sensitive dust/air mixture under specified test conditions. It is required for the assessment of ignition sources. The measurement can be conducted as follows:
-
Dispersed dust/air mixtures in the Hartmann tube according to DIN EN ISO/IEC 80079-20-2 (inductance 1 mH)
-
Dispersed dust/air mixtures in the Hartmann tube according to DIN EN ISO/IEC 80079-20-2 (inductance 1 mH and 0,1 mH)
-
Dispersed dust/air mixtures in the Hartmann tube at elevated temperatures according to DIN EN ISO/IEC 80079-20-2 (inductance 1 mH and 0,1 mH)
-
Hybride mixtuers
Flammability upon contact with water
The purpose of this test is to determine whether a substance reacts with water or moist air, producing dangerous amounts of flammable gases. The test is conducted as follows:
-
according to UN Test N.5 (GLP)
Ignitability
Qualitative tests are performed with various types of ignition sources to determine whether the test substance can ignite. The test is conducted as follows:
-
according to VDI 2263
Minimum ignition temperature of fluidized dust/air-mixtures
Determination of the ignition behavior of suspended dust/air mixtures on hot surfaces at ambient pressure. The minimum ignition temperature is the highest temperature at which dust/air mixtures do not ignite under the test conditions. The test is conducted as follows:
-
im BAM-Ofen nach DIN EN ISO/IEC 80079-20-2
Calorimetric properties
Using calorimetric properties, the heat release of chemical reactions and the thermal stability of substances and mixtures can be assessed. With our complementary calorimetric methods, we can investigate the heat release of chemical reactions under isothermal, isoperibolic, and adiabatic conditions. The use of modern reaction calorimeters allows for characterization under process-relevant conditions, as well as addressing complex storage and transport issues, such as storage in large tanks or assessing the thermal stability of polymerizable substances during maritime transport. From classical screening to individual process simulation, information can be provided. We offer the following methods for this purpose:
Differential Scanning Calorimetry
Dynamic differential calorimetry (DSC) is used to investigate the behavior of a sample as a function of temperature using a defined temperature program. The purpose of the testing procedure is to characterize the thermal stability and thermal potential of a substance or mixture by quantitatively determining heat quantities and characteristic temperatures. The measurement can be conducted under various crucible atmospheres and conforms to the following standards:
-
according to DIN 51005 (GLP)
-
according to DIN 51007 (GLP)
Simultaneous Differential-Calorimetry /Thermogravimetry
The purpose of this test is to obtain information about temperature-dependent changes in substances. Simultaneous heat conversion and mass changes resulting from physical transformations and chemical reactions are determined as a function of sample temperature and time.
-
according to DIN 51006
-
according to DIN 51007
Heat flow calorimetry using CPA 202 (reaction calorimetry)
The purpose of this test is to determine the thermal properties—particularly of reactive substances or mixtures—as well as to calculate the safety-related parameters derived from them for assessing the hazard potential of chemical reactions. These safety-related parameters include the reaction enthalpy in the broadest sense, heat output, possible accumulation, as well as the adiabatic temperature rise and specific heat.
Heat accumulation storage test
This testing procedure determines the minimum constant ambient air temperature at which thermally unstable substances are subjected to exothermic decomposition under packaging conditions. The determination of the Self-Accelerating Decomposition Temperature (SADT) or Self-Accelerating Polymerization Temperature (SAPT) is required for classification according to UN transport regulations and is representative of a 50 kg container.
-
according to UN Test H.4 (GLP)
Adiabatic calorimetry (Heat accumulation pressure vessel test and high pressure vessel test)
The pressure heat accumulation apparatus is an adiabatic calorimeter with low phi-factor. It allows for the simulation of continuous reactions under nearly adiabatic conditions. During the experiment, the temperature and pressure inside the measuring chamber are recorded. This measurement can determine storage stability, adiabatic induction time, maximum pressure and temperature, as well as their release rates. The design of the apparatus allows for the dosing of liquids, liquefied gases, and gases. In the high-pressure variant of the experimental setup, reactions can be monitored at pressures up to 300 bar.
Micro calorimetry using Thermal Activity Monitor (TAM)
With the help of microcalorimetry, heat flows in the range of a few µW/g to mW/g can be determined under isothermal conditions. This information is particularly necessary for assessing thermal stability over long storage periods or for evaluating stabilized substances and mixtures for transport and storage.
Calvet-Calorimetry using C80
The purpose of the testing procedure is to characterize the thermal stability and thermal potential of a substance or mixture by quantitatively determining heat quantities, characteristic temperatures, and pressures. Calvet calorimetry is a thermoanalytical method (more sensitive than DSC) in which the calorimetric effects of a sample are quantified by measuring the heat flow difference between the sample and an inert reference over the course of a predefined temperature-time program. The measurement cell is equipped with a pressure sensor, allowing for the determination of both the heat flow and the pressure profile during the measurement.
Micro Reaction Calorimetry
The method is used to determine thermal properties—particularly of reactive substances or mixtures—as well as to calculate the safety-related parameters derived from them for assessing the hazard potential of chemical reactions. These safety-related parameters include the reaction enthalpy in the broadest sense, heat output, the decay behavior of reactions, as well as the adiabatic temperature rise and specific heat. Furthermore, insights into pressure-influencing processes such as gas formation or vapor pressures can be derived from the measurements. Micro reaction calorimetry requires smaller sample quantities compared to conventional reaction calorimetry and provides an initial insight into the reaction behavior under isothermal conditions.
Explosibility of condensed substances
These parameters are used to characterize the explosibility of condensed substances and their classification for transport. A comprehensive series of measurements with various methods is necessary for assessing the explosibility of a substance. For this purpose, we offer the following testing methods:
Sensitivity to impact according to EG-Richtlinie 440/2008, Anhang A.14 (GLP)
The lowest impact energy at which an explosion just occurs is determined. An explosion is considered to have occurred if a bang or ignition is observed when the falling weight strikes the impact device.
Sensitivity to friction according to EG-Richtlinie 440/2008, Anhang A.14 (GLP)
A porcelain plate with 10 μl of the test substance is moved by a motor against a stationary porcelain pin with rough, spherical end surfaces. With different pin loads, forward and backward movements are performed over a distance of 1 cm each. It is observed whether the friction process causes an explosion.
Thermal sensitivity
The substance to be tested is heated in a cylindrical steel sleeve (approximately 30 ml capacity), which is sealed with a nozzle plate with a defined opening. The test determines the thermal sensitivity of the sample when heated under confinement. The test can be conducted according to the following regulations:
-
according to EG-Guideline 440/2008, Anhang A.14 (GLP)
-
according to UN Test 1(b), 2(b), E.1: Koenen-Test (GLP)
Lead block bulging according to Trauzel nach UN Test F.3 (GLP)
The test is a measurement method for determining the explosive power of the test substance
Deflagration test according to UN Test C.2 (GLP)
The deflagration capability of the substance or mixture is tested in an open vessel at atmospheric pressure.
Time pressure test according to UN Test 1(c), 2(b) und C.1 (GLP)
The 'Time/Pressure Test' (UN Manual, Test C.1) describes the deflagration behavior of the test substance under confinement
Sensitivity to detonation impact (2") according to UN-Gap-Test, 1(a), 2(a), A5
The method tests the detonability and sensitivity to detonation shocks. The determination can be performed at atmospheric pressure or at elevated pressures.
Unique facilities
Further to the equipment used for standard measurements, the Safety Engineering Laboratory of BASF SE has many unique and flexible facilities used for the development of safety concepts using tailor-made testing, these include:
- Bunker able to withstand an explosion of 5 kg TNTeq or 5 bar explosion pressure
- Chambers for calorimetric testing able to withstand an explosion of 100 g TNTeq or 10 bar explosion pressure
- 20 l sphere for gas explosion testing, capable of operating up to 500 °C and withstanding 600 bar explosion pressure
- 80 m3 climate-controlled chamber for electrostatics testing
- Highly flexible mixed low Phi-factor adiabatic calorimetry capable of measurements up to 350 °C and 300 bar, in batch, semi-batch or conti-mode, using different glass and metallic containers, with the possibility for tempered dosing, pressure relief, determination of temperature and pressure development with optional analysis of the composition of developed gases
- Various vessels, pipes and fittings of different pressure rating for gas-phase explosion testing
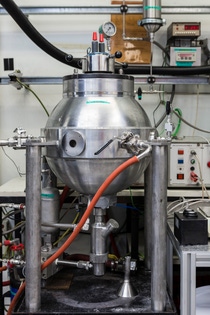
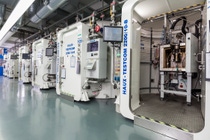
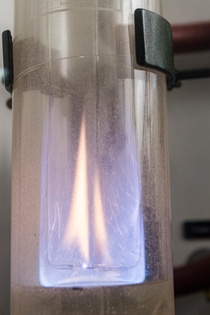
Responsibility towards our customers - our QM Certifications
By using our services, as a DIN ISO17025 accredited and GLP and DIN ISO9001 certified laboratory, you benefit from numerous aspects.
QM-Links
QM-Documents
- DAkkS Certificate (PL-14121-03-00)(only German)
Guarantee of highest quality standards - ISO 17025
Our accreditation according to DIN ISO17025 (for the scope of accreditation listed in the annex to our certificate PL-14121-03-00) guarantees that our test procedures and results comply with internationally recognized standards (ISO; ASTM, OECD, etc.). Our ability to achieve valid and reliable results at the highest technical level is regularly checked by external audits. In addition, we continuously take part in round robin tests with other testing laboratories in order to identify measurement deviations at an early stage. This means that you can rely on the quality of the measurements and tests we carry out. Our accreditation in accordance with DIN ISO 17025 guarantees you:
- Commitment to quality: Laboratories accredited to ISO 17025 must demonstrate a high level of technical competence and the ability to produce valid and reliable results. This leads to increased confidence in the quality of the measurements and tests performed.
- Traceability: Measurements carried out in ISO 17025 accredited laboratories are traceable to national or international standards. This traceability gives the results a certain credibility, as they can be traced back to recognized measurement standards.
- Confidentiality: In principle, every sample from a client is treated anonymously by the staff of the testing laboratory and the associated information, records and test reports are treated confidentially.
- International recognition: ISO 17025 is recognized worldwide, which means that our results are accepted and recognized worldwide, e.g. for product registrations or technical plant evaluations.
- Compliance with legal regulations: In many industries, there are specific legal requirements that necessitate the use of accredited laboratories for testing and calibration. ISO 17025 accreditation can ensure compliance with these regulations, avoiding potential legal issues and penalties.
- Increased customer confidence: Customers often prefer to work with us as an accredited laboratory because they can trust that the results obtained are accurate and reliable. Our staff are always available to answer any queries you may have about orders.
- Technical expertise: Accreditation requires that laboratories employ qualified staff and provide ongoing training. This ensures that employees have the necessary skills and knowledge to carry out tests and calibrations competently.
- Optimized processes: The accreditation process requires laboratories to implement robust management systems and standard operating procedures. This leads to more efficient processes, fewer errors and improved workflows, which ultimately improves service delivery.
- Continuous improvement: The standard encourages laboratories to regularly review and improve their processes and practices. This culture of continuous improvement can lead to better quality results and innovation in testing methods.
- Risk management: ISO 17025 accreditation helps laboratories to identify and mitigate the risks associated with testing and measurement procedures. This proactive approach can reduce the likelihood of errors and improve overall reliability.
Guarantee of highest quality standards – GLP
In addition to carrying out all measurement methods within the scope of accreditation, we also offer a wide range of our test methods within the scope of good laboratory practice. Good Laboratory Practice is a set of principles that ensure the quality and integrity of non-clinical laboratory studies. Among other things, this guarantees you accurate measurement results, complete documentation and multiple monitoring of the test order by different persons.
The overall benefits of GLP measurements are manifold and can have a significant impact on various aspects of research and regulatory compliance:
- Quality assurance: GLP provides a firm framework for maintaining high quality standards in laboratory practice. By adhering to GLP requirements, laboratories can ensure that their results are reliable, reproducible and traceable.
- Regulatory compliance: Many regulatory agencies require compliance with GLP regulations for studies submitted for product approvals where data integrity is of paramount importance. GLP-compliant measurements help companies meet these regulatory requirements and reduce the risk of delays or rejections due to non-compliance.
- Global recognition: GLP is internationally recognized and allows data to be accepted across borders. This is particularly beneficial for companies operating in multiple countries as it helps to ensure that their results are widely recognized.
- Integrity of the data: GLP requirements emphasize the importance of data management, including proper documentation and record keeping. This helps to protect against data tampering or loss and ensures that all results are correctly reported and validated. Both the order information and the measurement data obtained are archived in our test laboratory for at least 15 years and can be made available to the customer in the event of data loss.
- Standardization: GLP promotes the standardization of laboratory practices, which can facilitate comparisons between studies and improve the overall understanding of research results.
Find out more about our Fire Technology Lab and our Laborator for Materials Testing
We hope this information has helped you understand the benefits of testing with our accredited and GLP-certified laboratory, Prüflabor Sicherheitstechnik. Should you have any further questions, please do not hesitate to contact us.
67056 Ludwigshafen
Germany