Ludwigshafen
Working at full steam
A great deal of energy is required for chemical production. The Verbund structure ensures that energy is used particularly efficiently at the Ludwigshafen site. BASF’s aim is to ensure a secure and reliable supply of energy at competitive prices.
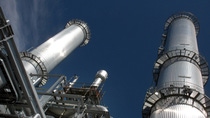
There is no production without energy. As well as electricity, in the chemical industry this also means steam in particular. BASF in Ludwigshafen requires a good 15 million metric tons of it every year. Roughly half of it comes from the three power plants at the site. In contrast to conventional power plants, which are only used to generate electricity, they also produce steam as well as electricity. The plants operate according to the principle of combined heat and power generation in which the primary energy is utilized particularly effectively: In the gas and steam turbine power plants, gas is initially burned in the gas turbines to generate electricity. The heat which is produced is then used to generate steam in downstream boilers. This is then also used in part to generate electricity. A large proportion of the steam goes to the production units at the site and is used as process steam in production, for example for drying products, heating reactors or for distillation.
But steam does not just come from the power plants. Roughly half of the demand is catered for from the Energy Verbund. The thermal energy that is produced in exothermic chemical reactions can be converted into steam and provided to other production units via pipelines.
Several thousand kilometers of cable supply the plant with power
Besides steam, large amounts of electrical energy are required at the Ludwigshafen site. The demand is approximately 4.5 terawatt hours (TWh) per year, a good one percent of all the power consumption in Germany. Many thousands of kilometers of cable, mostly laid underground, distribute the electricity around the site. Numerous transformers spread around the plant convert it to the voltage that is required in each of the production units. The electricity that is required in Ludwigshafen is also generated in the three power plants at the BASF site. The principle of combined heat and power generation is also proven to work here. These efficient and resource-friendly technologies allow BASF to cover largely all of its demand for power itself and remain competitive.