Zmiana dla klimatu
Zielony impuls dla świata chemii
Krakery parowe są sercem przemysłu chemicznego. Te wysokotemperaturowe piece gazowe są niezbędne do podstawowej produkcji chemicznej, jednak proces ten jest energochłonny i emituje znaczne ilości CO2. Aby sprostać wyzwaniom klimatycznym i energetycznym, BASF, Sabic i Linde rozpoczęły budowę pierwszego na świecie zakładu demonstracyjnego dla dużych krakerów parowych ogrzewanych elektrycznie w 2022. W kwietniu 2024 r. trzy firmy świętowały uruchomienie zakładu demonstracyjnego. Nasz cel w ramach tego projektu: Redukcja emisji CO2 jednego z najbardziej energochłonnych procesów produkcyjnych w przemyśle chemicznym o co najmniej 90% w porównaniu do powszechnie stosowanych dzisiaj technologii.
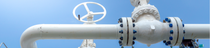
Pomysł: brać sobie do serca wszelkie zmiany
Wiele codziennych produktów powstaje z materiałów, które nie istniałyby bez krakerów parowych – pieców, które zwykle pracują w bardzo wysokich temperaturach, sięgających około 850°C. Piece te, znajdujące się na początku łańcucha wartości w chemii, rozkładają długie łańcuchy węglowodorów z surowego paliwa, jakim jest nafta. Ten proces prowadzi do powstania olefin i aromatów – chemikaliów stanowiących podstawę wielu produktów, takich jak witaminy, rozpuszczalniki, specjalistyczne chemikalia, tworzywa sztuczne czy leki.
Jednak obecnie proces krakingu parowego bazuje na paliwach kopalnych. Elektryfikacja pieców mogłaby zrewolucjonizować światowy przemysł chemiczny.
Podstawy: Nafta
Nafta uzyskiwana jest przez destylację ropy naftowej. Jest wykorzystywana do produkcji benzyny, ale również jest podstawą dla etylenu, propylenu, benzenu, toluenu i ksylenów. Wspólnie z metanolem i amoniakiem tworzą one siedem podstawowych chemikaliów, na których opiera się większość przemysłowej chemii organicznej.

Zakład BASF w Ludwigshafen dysponuje własnym portem. Z tego terminala główne składniki do produkcji chemicznej, takie jak nafta, metanol czy sprężone skroplone gazy, transportowane są rurociągami bezpośrednio do zakładów produkcyjnych lub zbiorników magazynowych.
Misja: wrócić do podstaw
Firma BASF wyznaczyła sobie ambitne cele i dąży na całym świecie do osiągnięcia zerowej emisji CO21 do 2050 roku. Aby ten cel zrealizować, konieczne jest przeorientowanie produkcji chemicznej na odnawialne źródła energii. Projekt eFurnace może znacząco wpłynąć na drogę przemysłu chemicznego w kierunku neutralności klimatycznej. Zakład demonstracyjny ma na celu ukazanie, że w porównaniu z konwencjonalnymi krakerami parowymi możliwe jest obniżenie emisji CO2 o co najmniej 90%. Wlicza się w to emisje Zakresu 1,2 i 3.1, uwzględniające bezpośrednie emisje z ogrzewania krakera parowego oraz emisje związane z parą i energią elektryczną.
Dowiedz się, jak redukujemy emisje
Więcej o naszych celach w zakresie ochrony klimatu
1 Cel obejmuje emisje z Zakresu 1,2 i 3.1. Inne gazy cieplarniane przeliczane są na równowartość CO2 zgodnie z protokołem dotyczącym emisji gazów cieplarnianych.
Budowa: integracja tego, co wydawało się niemożliwe
Budowa zakładu demonstracyjnego eFurnace rozpoczęła się w 2022 roku i została zakończona w kwietniu 2024 roku. Jeśli projekt się powiedzie, dowiedzie to, że energia elektryczna pochodząca z odnawialnych źródeł może skutecznie osiągnąć temperatury niezbędne do produkcji podstawowych chemikaliów. Testowane są równolegle dwa sposoby ogrzewania: bezpośredni, gdzie prąd elektryczny jest dostarczany bezpośrednio do rur procesowych w reaktorze, oraz pośredni, przy użyciu ciepła promieniującego z elementów grzewczych otaczających rury.
Prototyp zostanie w pełni zintegrowany w jednym z działających krakerów parowych w zakładzie BASF w Ludwigshafen. Firma BASF posiada również krakery parowe w Port Arthur (Teksas), Antwerpii (Belgia) oraz Nankin (Chiny).
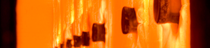
Cel: pilotażowa transformacja
Zakład demonstracyjny eFurnace będzie przetwarzał około czterech ton węglowodorów na godzinę. Zakład będzie korzystał z mocy rzędu sześciu megawatów odnawialnej energii – pochodzącej z wiatru, słońca oraz wody – aby przekształcać długie łańcuchy węglowodorów w olefiny i aromaty.
Ukazuje to ogromne zapotrzebowanie na energię potrzebną do pracy krakerów parowych oraz możliwe oszczędności emisji CO2, które można by osiągnąć, gdyby ten pilotażowy projekt okazał się sukcesem. Gdyby wszystkie krakersy parowe na całym świecie były ogrzewane zieloną energią elektryczną, miałoby to znaczący wpływ na zapotrzebowanie branży chemicznej na zieloną energię.
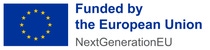
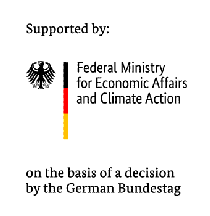
Przyszłość zielonej chemii: finansowanie zmian
Niemieckie Federalne Ministerstwo Gospodarki i Ochrony Klimatu dostrzegło ogromny potencjał projektu – rozwój demonstracyjnego zakładu eFurnace jest wspierany kwotą 14,8 miliona euro w ramach programu „Dekarbonizacja w Przemyśle”. Program ten pomaga niemieckim przedsiębiorstwom energochłonnym w dążeniu do neutralności węglowej. Projekt jest finansowany przez Unię Europejską w ramach programu NextGenerationEU.
Misją BASF jest osiągnięcie zerowej emisji CO2 oraz elektryfikacja wysoce energochłonnego krakera parowego, co jest znaczącym kamieniem milowym w naszej drodze transformacji.
BASF „Verbund”: efektywne wykorzystanie zasobów
„Verbund” po niemiecku oznacza „być połączonym”. Dla BASF zrównoważony rozwój to już rzeczywistość. W naszych unikatowych lokalizacjach Verbund, instalacje produkcyjne, przepływ energii, logistyka i infrastruktura zostały połączone w inteligentny sposób, co pozwala nam efektywniej korzystać z energii i oszczędzać zasoby. Produkty uboczne z jednego procesu są wykorzystywane jako surowce dla innych. Nie tylko zmniejsza to emisje, ale także obniża koszty logistyki. Inteligentne sieci umożliwiają również optymalne dostarczanie energii w naszych zakładach. Na przykład ciepło odpadowe z procesu produkcyjnego w jednym zakładzie jest wykorzystywane jako energia w innych zakładach.
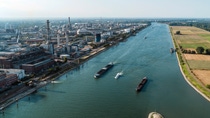
BASF posiada sześć zakładów Verbund na całym świecie, zlokalizowanych w Europie, Ameryce Północnej i Azji. Są to główne centra produkcji, dostarczające ponad połowę produktów BASF. BASF posiada też 233 inne zakłady produkcyjne.
Dowiedz się więcej o zielonej chemii w BASF:
Sfinansowane przez Unię Europejską – NextGenerationEU. Wyrażone poglądy i opinie są wyłącznie poglądami autora i niekoniecznie odzwierciedlają poglądy Unii Europejskiej lub Komisji Europejskiej. Ani Unia Europejska, ani Komisja Europejska nie ponoszą za nie odpowiedzialności.